Heat-dissipating powder coating modifying aid and preparation method thereof
A powder coating and modification technology, applied in the direction of coating, can solve the problems of weak surface adhesion, small application range, unsatisfactory use effect, etc., to improve the mechanical properties of materials, enhance thermal conductivity, and improve wear resistance. Effect
- Summary
- Abstract
- Description
- Claims
- Application Information
AI Technical Summary
Problems solved by technology
Method used
Image
Examples
preparation example Construction
[0020] Preparation of Modified Auxiliary Materials for Heat Dissipating Coatings
[0021] Each raw material is weighed according to the following parts by weight: 25 parts of nano kaolinite, 3 parts of corundum, 9 parts of phosphate rock, 6 parts of polyacrylate, 6 parts of aluminum dihydrogen phosphate, 6 parts of light calcium carbonate, silane dihydrogen 1.3 parts of joint agent, 0.4 parts of isothiazolinone, enter the preparation process after weighing:
[0022] A. Calcining nano-kaolinite and corundum at 750° C. for 1 hour, mixing and grinding them with light calcium carbonate after discharging to obtain premix a;
[0023] B. Mix phosphate rock and aluminum dihydrogen phosphate for ball milling, add polyacrylate during the ball milling process, and keep stirring at 85°C for 8 minutes to obtain premix b;
[0024] C. Mix premix a and premix b, add the remaining raw materials, and stir and disperse;
[0025] D. Drying to obtain paint modification additives for later use. ...
Embodiment 1-3
[0037] Embodiment 1-3—powder coating for radiator shell
[0038] A powder coating for the outer shell of a radiator, which is composed of the following raw materials in parts by weight: 60 parts of E-44 epoxy resin, 15 parts of montmorillonite powder, 2 parts of ethylene bisstearamide, 2 parts of anti-scorch agent CTP, tetramethyl 3 parts of oxymethyl glycoluril, 2 parts of phthalic anhydride, 6 parts of quasi-spherical silica powder, 3 parts of hollow glass microspheres, 2 parts of polyvinylpyrrolidone, 0.2 parts of tert-butyl peroxyacetate, dimethylaminopropylamine 10 parts, 4 parts of ethylene glycol, and 10 parts of heat-dissipating modified additives.
[0039] Mix the above montmorillonite powder with ethylene glycol, stir well, add quasi-spherical silica powder, keep the temperature at 40°C, stir and mix thoroughly, add tert-butyl peroxyacetate, stir and disperse at 2000 rpm for 6 minutes, add the remaining The raw materials are melted and extruded through an extruder, ...
PUM
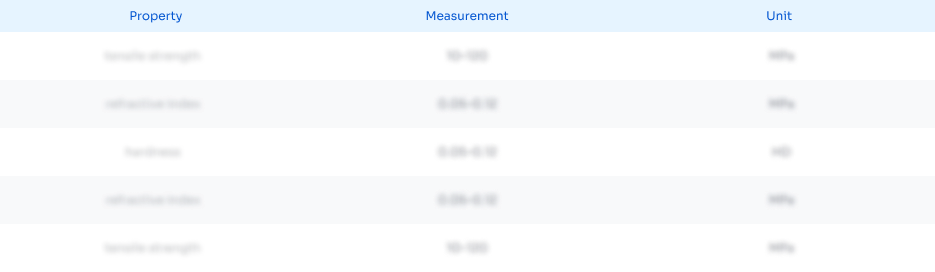
Abstract
Description
Claims
Application Information

- R&D
- Intellectual Property
- Life Sciences
- Materials
- Tech Scout
- Unparalleled Data Quality
- Higher Quality Content
- 60% Fewer Hallucinations
Browse by: Latest US Patents, China's latest patents, Technical Efficacy Thesaurus, Application Domain, Technology Topic, Popular Technical Reports.
© 2025 PatSnap. All rights reserved.Legal|Privacy policy|Modern Slavery Act Transparency Statement|Sitemap|About US| Contact US: help@patsnap.com