A light full-hydraulic drilling rig for underground drilling in coal mines
A fully hydraulic, lightweight technology, applied in rotary drilling rigs, drilling equipment and methods, drill pipes, etc., can solve the problems of alignment difficulties, the impact of user safety production, and increased drilling rig vibration, so as to improve alignment difficulties, Improve the effect of cracking failure and prolong service life
- Summary
- Abstract
- Description
- Claims
- Application Information
AI Technical Summary
Problems solved by technology
Method used
Image
Examples
Embodiment Construction
[0088] Such as figure 1 , figure 2 with image 3 As shown, the present invention comprises frame 6, drilling rod 3 and water braid 2, and the guide rail 8 that is fixedly connected on the top of frame 6, propulsion hydraulic cylinder 5 and hydraulic clamp 4, and the described guide rail 8 is slidably connected with drilling rig Power head 1; the drill pipe 3 is connected to the drill power head 1 through the water braid 2 connected to the drill power head 1 after passing through the hydraulic clamp 4 and the water braid 2;
[0089] Such as Figure 4 , Figure 5 with Image 6 As shown, the hydraulic clamper 4 includes a clamper base 21 fixedly connected to the frame 6 and a support base 19 fixedly connected to the top of the clamper base 21, the support base 19 is an integral structure, and the The geometric center position of the support base 19 is provided with a central hole for the drill rod 3 to pass through, and the top surface, the left side and the right side of t...
PUM
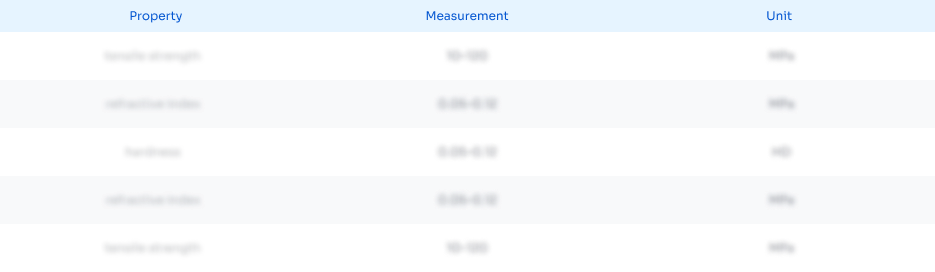
Abstract
Description
Claims
Application Information

- R&D
- Intellectual Property
- Life Sciences
- Materials
- Tech Scout
- Unparalleled Data Quality
- Higher Quality Content
- 60% Fewer Hallucinations
Browse by: Latest US Patents, China's latest patents, Technical Efficacy Thesaurus, Application Domain, Technology Topic, Popular Technical Reports.
© 2025 PatSnap. All rights reserved.Legal|Privacy policy|Modern Slavery Act Transparency Statement|Sitemap|About US| Contact US: help@patsnap.com