Crucible cover plate for polysilicon ingot furnace and cover plate surface coating method
A polycrystalline silicon ingot furnace and crucible cover technology, which is applied to the growth of polycrystalline materials, chemical instruments and methods, crystal growth, etc., can solve the problem of reducing the service life of graphite crucibles and carbon/carbon cover plates, affecting the yield and quality of polycrystalline silicon, and increasing The number of carbon hard points and other issues can achieve the effect of low cost per heat, lower carbon content, and lower damage
- Summary
- Abstract
- Description
- Claims
- Application Information
AI Technical Summary
Problems solved by technology
Method used
Image
Examples
Embodiment Construction
[0023] The crucible cover plate and cover plate surface coating method for polysilicon ingot furnace provided by the present invention, by setting SiC coating 2 on the outer surface of carbon / carbon composite material cover plate 1 to reduce the carbon content of polysilicon ingot, extend the cover plate service life.
[0024] The preparation method of the SiC coating on the surface of the crucible cover plate for polysilicon ingot casting furnace of the present invention adopts the process method of combining chemical vapor deposition and high temperature treatment to prepare a dense SiC coating with good bonding force on the surface of the crucible, a preferred implementation The process is as follows:
[0025] 1) Cleaning and drying: Use running water to clean the floating dust on the surface of the carbon / carbon composite cover plate, and then use an ultrasonic instrument to clean it 2 to 3 times, 30 minutes each time. Put it in an oven at 200°C for more than 2 hours, and...
PUM
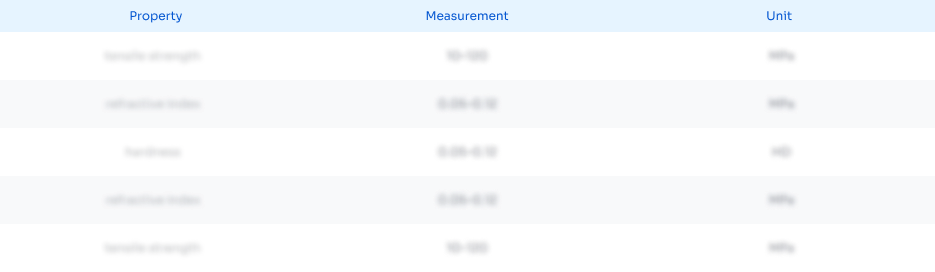
Abstract
Description
Claims
Application Information

- Generate Ideas
- Intellectual Property
- Life Sciences
- Materials
- Tech Scout
- Unparalleled Data Quality
- Higher Quality Content
- 60% Fewer Hallucinations
Browse by: Latest US Patents, China's latest patents, Technical Efficacy Thesaurus, Application Domain, Technology Topic, Popular Technical Reports.
© 2025 PatSnap. All rights reserved.Legal|Privacy policy|Modern Slavery Act Transparency Statement|Sitemap|About US| Contact US: help@patsnap.com