Large-area large-thickness TU2 copper/steel explosion composite material and defect repairing method
A technology of composite materials and repair methods, which is applied in the field of copper composite materials, can solve problems such as reducing repair costs, and achieve the effects of strong economic practicability, simple process and operation process
- Summary
- Abstract
- Description
- Claims
- Application Information
AI Technical Summary
Problems solved by technology
Method used
Image
Examples
Embodiment 1
[0017] Material TU2+Q235B, size (6+34)×900×1800mm; non-fitting size 70×250mm, the position is that the edge is not pasted.
[0018] 1. Groove design and processing, using a grinder, cutting down to the carbon steel layer along the pre-marked line, removing the unattached copper plate, and removing 2-2.5mm of the Q235B plate with a 60# grinding wheel, of which The two right angles are polished with a stainless steel grinding head, and a 120° bevel is ground on the three sides of the cladding.
[0019] 2. Transition layer surfacing welding process, using argon arc welding, using φ2.4ERNi-1 welding wire, welding with 120A current for the first layer and 110A current for the second layer. After the surfacing welding is completed, the processing is flush with the joint surface.
[0020] 3. The overall heating process uses a heating rate of 100°C / h to heat the copper-steel composite plate to 480°C and keep it warm for 30 minutes.
[0021] 4. Gradient thermal insulation process, pre...
Embodiment 2
[0024] Material TU2+Q235B, size (10+20)×2100×6000mm; non-fitting is a circle of φ50mm, and the position is that the middle part is not pasted.
[0025] 1. Groove design and processing, use a grinder, cut down to the carbon steel layer along the pre-marked line, remove the unattached copper plate, and remove 2-2.5mm of the Q235B plate with a 60# grinding wheel, of which The circular joint surface is ground with a stainless steel grinding head, and a 120° bevel is ground on the circumference of the cladding.
[0026] 2. The surfacing welding process of the transition layer uses the argon arc welding method, uses φ2.4ERNiCu-7 welding wire, and welds with a current of 130A for the first layer and a current of 120A for the second layer. After the surfacing is completed, the grinding is flush with the joint surface.
[0027] 3. The overall heating process uses a heating rate of 100°C / h to heat the copper-steel composite plate to 600°C and keep it warm for 20 minutes.
[0028] 4. Gr...
PUM
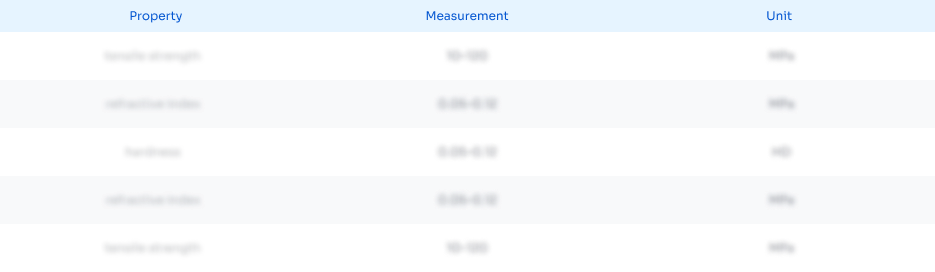
Abstract
Description
Claims
Application Information

- R&D Engineer
- R&D Manager
- IP Professional
- Industry Leading Data Capabilities
- Powerful AI technology
- Patent DNA Extraction
Browse by: Latest US Patents, China's latest patents, Technical Efficacy Thesaurus, Application Domain, Technology Topic, Popular Technical Reports.
© 2024 PatSnap. All rights reserved.Legal|Privacy policy|Modern Slavery Act Transparency Statement|Sitemap|About US| Contact US: help@patsnap.com