Fireproof heat-insulation silicon rubber and preparation method thereof
A technology of silicone rubber and additives, which is applied in the field of fire-proof and heat-insulating silicone rubber and its preparation
- Summary
- Abstract
- Description
- Claims
- Application Information
AI Technical Summary
Problems solved by technology
Method used
Image
Examples
preparation example Construction
[0064] A preparation method of fireproof and heat-insulating silicone rubber, comprising the following steps:
[0065] Step 1: Use a double-roll mill to adjust the roller distance to 3-5mm, and add the base material at a certain roller temperature;
[0066] Step 2: Add reinforcing agent, other additives, flame retardant and high-temperature-resistant functional fillers to the double-roller mill in sequence, mix and heat-treat after mixing;
[0067] Step 3: After the heat treatment is completed, after the temperature drops to room temperature, add other additives in the double-roll mill, and thin the film through multiple times;
[0068] Step 4: After the lower piece is parked for 24 hours, vulcanize it with a flat vulcanizing machine to make a fire-proof and heat-insulating silicone rubber sample.
[0069] The substrate in step 1 is 100 parts of phenyl silicone rubber;
[0070]The reinforcing agent in step 2 is 30 parts of meteorological silica; Described other additives a...
Embodiment
[0077] Using a double-roll mill, adjust the roll distance to 3-5 mm, add 100 grams of phenyl silicone rubber at a temperature of 0-50 ° C, then add 30 grams of meteorological white carbon black, diphenylsilanediol 4 grams, 10 grams of melamine polyphosphate, 30 grams of aluminum hydroxide, 12 grams of silicon carbide, and 10 grams of boron nitride, mixed for 20 minutes and then heat treated at 200°C for 1 hour. After the heat treatment is completed, wait until the temperature drops to room temperature , add 1 gram of vulcanizing agent dicumyl peroxide to the open mill, thin pass 3 times and take off the tablet; after parking for 24 hours, vulcanize with a flat vulcanizer at 10MPa, 160°C for 10 minutes to make a test sample.
[0078] The fire-proof test of the fire-proof and heat-insulating silicone rubber sample prepared by the above method is as follows:
[0079] 1. 3000K ablation test
[0080] ⑴. Test condition: 3000K×20s
[0081] ⑵. Test method: GJB323A-96
[0082] ⑶. ...
PUM
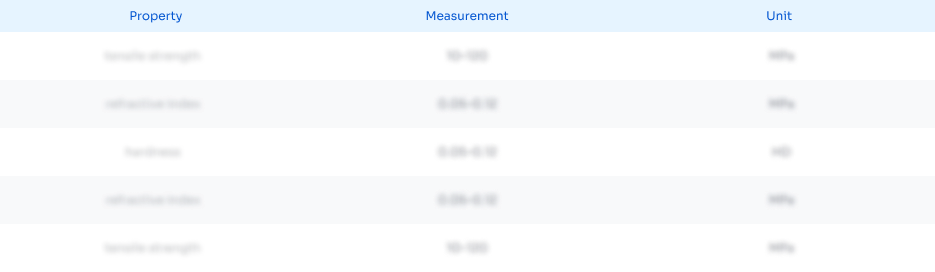
Abstract
Description
Claims
Application Information

- R&D
- Intellectual Property
- Life Sciences
- Materials
- Tech Scout
- Unparalleled Data Quality
- Higher Quality Content
- 60% Fewer Hallucinations
Browse by: Latest US Patents, China's latest patents, Technical Efficacy Thesaurus, Application Domain, Technology Topic, Popular Technical Reports.
© 2025 PatSnap. All rights reserved.Legal|Privacy policy|Modern Slavery Act Transparency Statement|Sitemap|About US| Contact US: help@patsnap.com