A New Production Process of Resin Code Disc
A production process and code disc technology, which is applied in the production process of new resin code discs, can solve the problems of easy peeling off of the metal layer, corrosion of the metal layer, poor light transmittance of the resin material, etc., and achieve good environmental friendliness and adaptability Improved effect
- Summary
- Abstract
- Description
- Claims
- Application Information
AI Technical Summary
Problems solved by technology
Method used
Image
Examples
Embodiment Construction
[0028] The process implementation of this patent can be divided into two major parts, that is, the metal nickel master plate production process and the replication process of the resin code disc, which are specifically described as follows.
[0029] mastering
[0030] Materials needed for mastering:
[0031] 1) A glass substrate whose surface needs to be optically polished.
[0032] 2) The photoresist uses S1805 photoresist of SHIPLY company, and the photoresist solvent uses EC-SOLVENT of SHIPLY company. The ratio is 1:5.
[0033] 3) The adhesive uses 1% by volume disilane aqueous solution.
[0034] 4) The ratio of the developer solution is: 20 grams of sodium hydroxide and 100 grams of sodium pyrophosphate mixed with 8 liters of water.
[0035] 5) The sputtering process is used for metallization, and the nickel-vanadium target is used, and the ratio of the two is 1:99.
[0036] 6) The electroforming process uses nickel sulfide nickel balls as raw materials.
[0037] The...
PUM
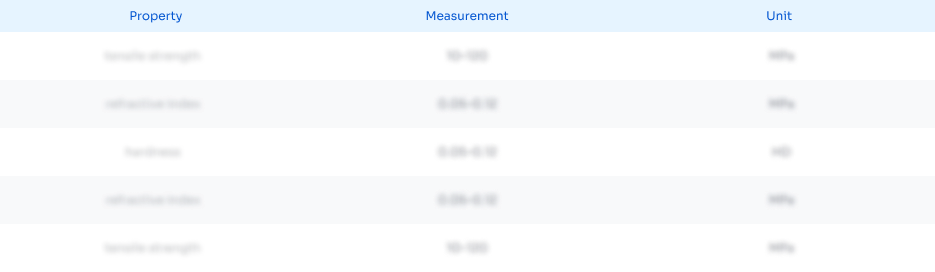
Abstract
Description
Claims
Application Information

- R&D
- Intellectual Property
- Life Sciences
- Materials
- Tech Scout
- Unparalleled Data Quality
- Higher Quality Content
- 60% Fewer Hallucinations
Browse by: Latest US Patents, China's latest patents, Technical Efficacy Thesaurus, Application Domain, Technology Topic, Popular Technical Reports.
© 2025 PatSnap. All rights reserved.Legal|Privacy policy|Modern Slavery Act Transparency Statement|Sitemap|About US| Contact US: help@patsnap.com