Manufacturing technology for resin lens with high refraction index and high abbe number
A high Abbe number, resin lens technology, applied in the field of lens manufacturing, can solve problems that affect consumer choices, expensive product prices, severe dispersion, etc.
- Summary
- Abstract
- Description
- Claims
- Application Information
AI Technical Summary
Problems solved by technology
Method used
Image
Examples
Embodiment 1
[0047] formula:
[0048]
[0049] The above is the formula for determining the dosage of ingredients per 1000 g of the resin lens of this embodiment.
[0050] Among them, component A (KOC KR70WA) is bis(2,3-epithiopropyl) sulfide, and component B (KOC KR70WAB) is composed of 63.7g dimercaptoethyl sulfide and 1.3g 2-(2-mercaptoethyl) thio)ethanol, component C (KOC KR70WC) is isophorone diisocyanate.
[0051] The resin lens preparation process of the present embodiment is as follows:
[0052] (1) Mold cleaning and assembly: After cleaning the mold, assemble the mold under the condition of 0.6MPa air pressure. Put the mold into the mold cleaning machine for cleaning, and the cleaning process is shown in the table below:
[0053]
[0054] During this process, it is necessary to use a sugar content meter to measure the concentration of the cleaning solution every 2 hours. If the sugar content is lower than the process value of 10-12, add cleaning solution until it meets th...
Embodiment 2
[0072] formula:
[0073]
[0074] The above is the formula for determining the dosage of ingredients per 1000 g of the resin lens of this embodiment.
[0075] Among them, component A (KOC KR70WA) is bis(2,3-epithiopropyl) sulfide, and component B (KOC KR70WAB) is composed of 47.7g dimercaptoethyl sulfide and 5.3g 2-(2-mercaptoethyl) thio)ethanol, component C (KOC KR70WC) is isophorone diisocyanate; release agent (HILUB 70) consists of 0.784g isophorone diisocyanate, 0.008g poly(oxy-1,2- Ethyl)-A-branched nonylphenyl-Ω-hydroxyl-phosphate and 0.008g polyethylene glycol monoalkyl ether.
[0076]The preparation process of the resin lens in this embodiment is as follows: after cleaning the mold, assemble the mold under the condition of 0.6MPa air pressure; add 65g KOC KR70WB, 50g KOC KR70WC and 6.0g HIUA-31A into the sealed batching barrel at a temperature of 28-30°C Stir for 1 hour under the same conditions, and mix evenly to obtain a mixed liquid material; after the temperat...
Embodiment 3
[0080] formula:
[0081]
[0082] The above is the formula for determining the dosage of ingredients per 1000 g of the resin lens of this embodiment.
[0083] Among them, component A (KOC KR70WA) is bis(2,3-epithiopropyl) sulfide, and component B (KOC KR70WAB) is composed of 59.4g dimercaptoethyl sulfide and 0.6g 2-(2-mercaptoethyl) thio)ethanol, component C (KOC KR70WC) is isophorone diisocyanate; release agent (HILUB 70) consists of 0.57g isophorone diisocyanate, 0.018g poly(oxy-1,2- Ethyl)-A-branched nonylphenyl-Ω-hydroxyl-phosphate and 0.012g polyethylene glycol monoalkyl ether.
[0084] The lens is manufactured according to the method of Example 1, and its performance is tested, the results are shown in the following table:
[0085] Test items
PUM
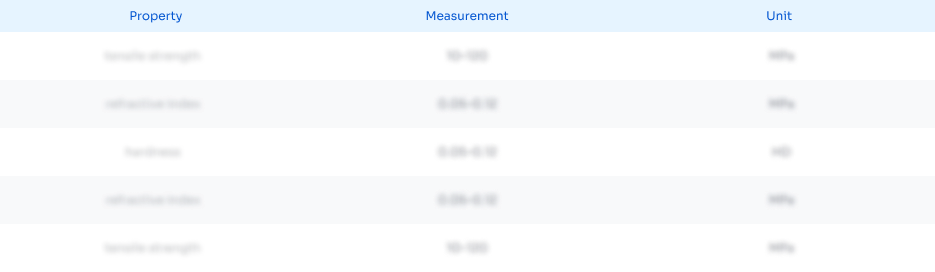
Abstract
Description
Claims
Application Information

- R&D
- Intellectual Property
- Life Sciences
- Materials
- Tech Scout
- Unparalleled Data Quality
- Higher Quality Content
- 60% Fewer Hallucinations
Browse by: Latest US Patents, China's latest patents, Technical Efficacy Thesaurus, Application Domain, Technology Topic, Popular Technical Reports.
© 2025 PatSnap. All rights reserved.Legal|Privacy policy|Modern Slavery Act Transparency Statement|Sitemap|About US| Contact US: help@patsnap.com