Orthorhombic three-freedom joint driven by pneumatic artificial muscles
A pneumatic artificial muscle and artificial muscle technology, applied in the field of orthogonal three-degree-of-freedom joints, can solve the problems of small working space, large volume, large joint volume, etc., and achieve the effect of small size and light weight
- Summary
- Abstract
- Description
- Claims
- Application Information
AI Technical Summary
Problems solved by technology
Method used
Image
Examples
Embodiment Construction
[0014] The present invention will be further described below in conjunction with the accompanying drawings.
[0015] Such as figure 1 As shown, two of the rotation axes of the three directions of the joint in the present invention are perpendicular to each other, and through a coordinate origin, the orthogonality is realized. Take the center of the cross axis as the coordinate origin O, establish a motion coordinate system O-XYZ in the joint, and the origin O coincides with the origin of the fixed coordinate system, establish the X axis with the rotation axis of the bottom bracket as the axis, and use the rotation of the upper bracket The Y-axis is established as the axis, and the Z-axis is established as the rotation axis of the end effector, so that simple kinematic analysis can be performed on the joint.
[0016] Such as figure 2 As shown, an orthogonal three-degree-of-freedom joint driven by pneumatic artificial muscles is mainly composed of a U-shaped X-axis bracket 6,...
PUM
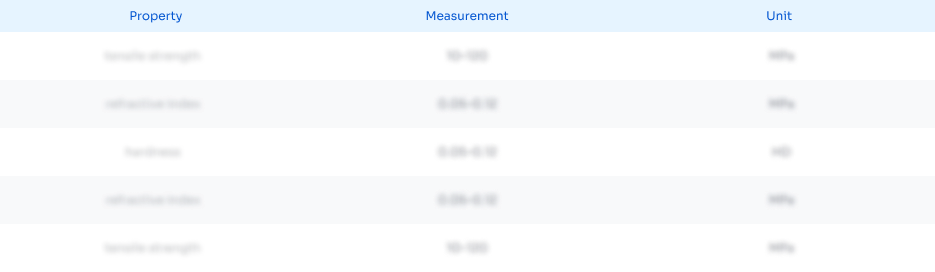
Abstract
Description
Claims
Application Information

- R&D Engineer
- R&D Manager
- IP Professional
- Industry Leading Data Capabilities
- Powerful AI technology
- Patent DNA Extraction
Browse by: Latest US Patents, China's latest patents, Technical Efficacy Thesaurus, Application Domain, Technology Topic, Popular Technical Reports.
© 2024 PatSnap. All rights reserved.Legal|Privacy policy|Modern Slavery Act Transparency Statement|Sitemap|About US| Contact US: help@patsnap.com