Polytetrafluoroethylene film for capacitor
A PTFE and capacitor technology, applied in the field of PTFE film for capacitors, can solve the problems of film foil gap, film breakage, high scrap rate, etc., to improve tensile resistance, prolong service life, and form film good effect
- Summary
- Abstract
- Description
- Claims
- Application Information
AI Technical Summary
Problems solved by technology
Method used
Examples
Embodiment 1
[0016] In this embodiment, a polytetrafluoroethylene film for capacitors is composed of the following components in parts by weight: 120 parts of polytetrafluoroethylene, 12 parts of triethanolamine, 2 parts of polyvinylidene fluoride, and 4 parts of calcium stearate , 20 parts of polyoxyethylene lauryl ether, 12 parts of polyacrylamide, 2 parts of glyceryl monostearate, 0.5 parts of diphenyl ethyl ketone, 1 part of dicumyl hydroperoxide and 4 parts of film former.
[0017] Wherein, the film-forming agent is polyurethane resin, polyvinyl alcohol, lauryl acetic alcohol and chitosan. The parts by weight of each component of the film-forming agent are respectively 15 parts of polyurethane resin, 5 parts of polyvinyl alcohol, 1 part of dodecyl acetic alcohol and 0.5 part of chitosan.
Embodiment 2
[0019] In this embodiment, a polytetrafluoroethylene film for capacitors is composed of the following components in parts by weight: 100 parts of polytetrafluoroethylene, 10 parts of triethanolamine, 5 parts of polyvinylidene fluoride, and 1 part of calcium stearate , 24 parts of polyoxyethylene lauryl ether, 10 parts of polyacrylamide, 6 parts of glyceryl monostearate, 1.5 parts of diphenyl ethyl ketone, 3 parts of dicumyl hydroperoxide and 9 parts of film former.
[0020] Wherein, the film-forming agent is polyurethane resin, polyvinyl alcohol, lauryl acetic alcohol and chitosan. The parts by weight of each component of the film forming agent are respectively 9 parts of polyurethane resin, 3 parts of polyvinyl alcohol, 4 parts of dodecyl acetic alcohol and 2.5 parts of chitosan.
Embodiment 3
[0022] In this embodiment, a polytetrafluoroethylene film for capacitors is composed of the following components in parts by weight: 110 parts of polytetrafluoroethylene, 11 parts of triethanolamine, 4 parts of polyvinylidene fluoride, and 2 parts of calcium stearate , 22 parts of polyoxyethylene lauryl ether, 11 parts of polyacrylamide, 5 parts of glyceryl monostearate, 1.2 parts of diphenyl ethyl ketone, 2 parts of dicumyl hydroperoxide and 7 parts of film former.
[0023] Wherein, the film-forming agent is polyurethane resin, polyvinyl alcohol, lauryl acetic alcohol and chitosan. The parts by weight of each component of the film-forming agent are respectively 12 parts of polyurethane resin, 4 parts of polyvinyl alcohol, 2 parts of dodecyl acetic alcohol and 2 parts of chitosan.
PUM
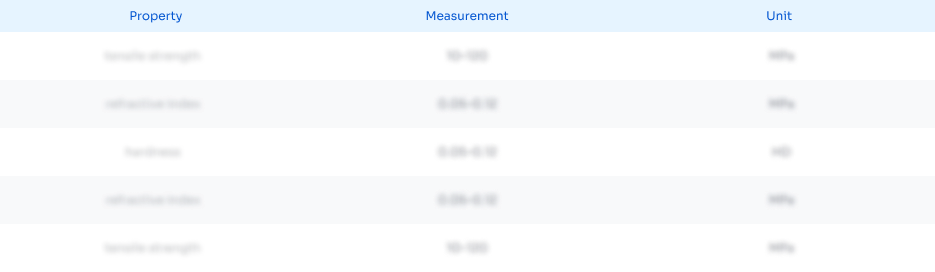
Abstract
Description
Claims
Application Information

- R&D
- Intellectual Property
- Life Sciences
- Materials
- Tech Scout
- Unparalleled Data Quality
- Higher Quality Content
- 60% Fewer Hallucinations
Browse by: Latest US Patents, China's latest patents, Technical Efficacy Thesaurus, Application Domain, Technology Topic, Popular Technical Reports.
© 2025 PatSnap. All rights reserved.Legal|Privacy policy|Modern Slavery Act Transparency Statement|Sitemap|About US| Contact US: help@patsnap.com