Preparation method for thin film used for DBR
A thin-film preparation and thin-film technology, which is applied in the field of DBR thin-film preparation, can solve the problems of slow film rate and impact on production capacity, and achieve the effect of increasing production capacity and improving deposition efficiency
- Summary
- Abstract
- Description
- Claims
- Application Information
AI Technical Summary
Problems solved by technology
Method used
Image
Examples
Embodiment Construction
[0023] In order to make the technical solution of the present invention clearer, the present invention will be further described in detail below in conjunction with the accompanying drawings and specific embodiments.
[0024] see figure 1 , a kind of film preparation method for DBR, comprises the steps:
[0025] S100, within the first preset time, after filling the process chamber with oxygen according to the first flow rate value, put the substrate into the process chamber;
[0026] S200, continue to fill the process chamber with oxygen according to the first flow rate value, and simultaneously deposit a thin film for DBR on the upper surface of the substrate for a second preset time;
[0027] S300, filling the process chamber with oxygen according to the second flow value, and simultaneously depositing a thin film for DBR on the upper surface of the substrate for a third preset time, wherein the second flow value is less than the first flow value;
[0028] S400, return to ...
PUM
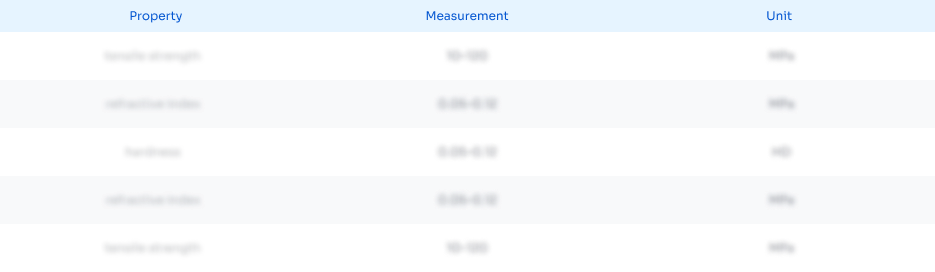
Abstract
Description
Claims
Application Information

- R&D
- Intellectual Property
- Life Sciences
- Materials
- Tech Scout
- Unparalleled Data Quality
- Higher Quality Content
- 60% Fewer Hallucinations
Browse by: Latest US Patents, China's latest patents, Technical Efficacy Thesaurus, Application Domain, Technology Topic, Popular Technical Reports.
© 2025 PatSnap. All rights reserved.Legal|Privacy policy|Modern Slavery Act Transparency Statement|Sitemap|About US| Contact US: help@patsnap.com