Preparing method of tungsten copper powder for perforating bullet type cover
A powder preparation, tungsten copper technology, applied in coating and other directions, can solve problems such as low production efficiency and increased production cost, and achieve the effects of avoiding pollution, improving friction, and reducing molding pressure
- Summary
- Abstract
- Description
- Claims
- Application Information
AI Technical Summary
Problems solved by technology
Method used
Examples
Embodiment 1
[0022] Example 1: 1.5% (mass percent) copper coated with tungsten powder
[0023] Weigh 1.882Kg of copper acetate and put it into a ball mill, add 6Kg of cemented carbide balls and mill for 1.5 hours, then add 40Kg of tungsten powder and mix for 2 hours at a speed of 300 rpm. Subsequently, 400 mm of water was added to continue ball milling for 30 minutes. Put the powder mixture into a boat and slowly push it into a 450°C hydrogen reduction furnace to calcine and reduce the powder. After coming out of the furnace, put 40.6Kg of copper-coated tungsten powder and 9.4Kg of electrolytic copper powder into the ball mill, add 6Kg of hard alloy balls and 40 grams of engine oil. The speed of the ball mill is 300 rpm, and the powder is unloaded after mixing for 2 hours. The prepared tungsten-copper mixed powder is formed into a powder cover according to the normal spinning process, and assembled in the SDP39HMX25-2 perforating charge, with a penetration depth of 810mm.
Embodiment 2
[0024] Embodiment 2: Tungsten powder coating 1% (mass percentage) copper
[0025] Weigh 1.255Kg of copper acetate and put it into a ball mill, add 6Kg of cemented carbide balls and mill for 1 hour, then add 40Kg of tungsten powder and mix for 2 hours at a speed of 300 rpm. Subsequently, 400 mm of water was added to continue ball milling for 30 minutes. Put the powder mixture into a boat and slowly push it into a 450°C hydrogen reduction furnace to calcine and reduce the powder. After coming out of the furnace, put 40.4Kg of copper-coated tungsten powder and 9.6Kg of electrolytic copper powder into the ball mill, add 5Kg of hard alloy balls and 40 grams of engine oil. The engine oil is ordinary engine oil. The speed of the ball mill is 300 rpm, and the powder is unloaded after mixing for 2 hours. The prepared tungsten-copper mixed powder is formed into a powder cover according to the normal spinning process, and assembled in the SDP39HMX25-2 perforating bullet, with a penetr...
PUM
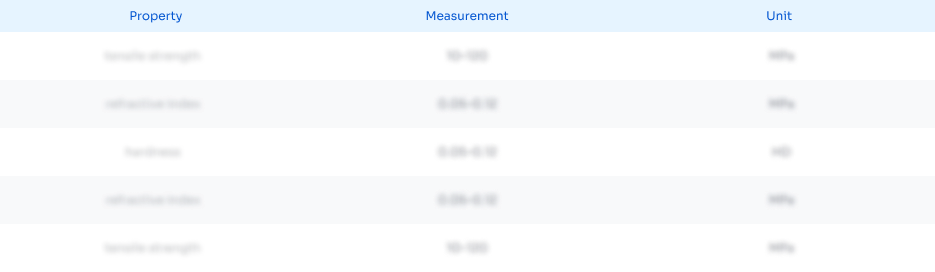
Abstract
Description
Claims
Application Information

- R&D Engineer
- R&D Manager
- IP Professional
- Industry Leading Data Capabilities
- Powerful AI technology
- Patent DNA Extraction
Browse by: Latest US Patents, China's latest patents, Technical Efficacy Thesaurus, Application Domain, Technology Topic, Popular Technical Reports.
© 2024 PatSnap. All rights reserved.Legal|Privacy policy|Modern Slavery Act Transparency Statement|Sitemap|About US| Contact US: help@patsnap.com