A film winding tension control system and method based on FPGA
A technology of tension control and control algorithm, which is applied in the directions of winding strips, thin material processing, transportation and packaging, etc., can solve problems such as difficult to achieve high control accuracy, high requirements for operators, and inability to realize automatic control. Achieve the effect of improving data parallel processing capability, short development cycle, and easy hardware parallel implementation
- Summary
- Abstract
- Description
- Claims
- Application Information
AI Technical Summary
Problems solved by technology
Method used
Image
Examples
Embodiment Construction
[0038] In order to make the purpose and technical solution of the present invention clearer, the present invention will be further described in detail below in conjunction with the accompanying drawings and embodiments. Here, the specific implementation manners and descriptions of the present invention are used to explain the present invention, but not to limit the present invention.
[0039] see figure 2 , the present invention is a film winding tension control system based on FPGA, which is a closed-loop fuzzy self-adaptive PID control system. The control system includes a tension signal acquisition module for detecting film winding tension, an FPGA control chip Film winding tension control module, film winding module with brushless DC motor and upper computer operation panel for setting system initial value and displaying film tension. Among them, the output end of the tension signal acquisition module is connected to the signal input end of the film winding tension contr...
PUM
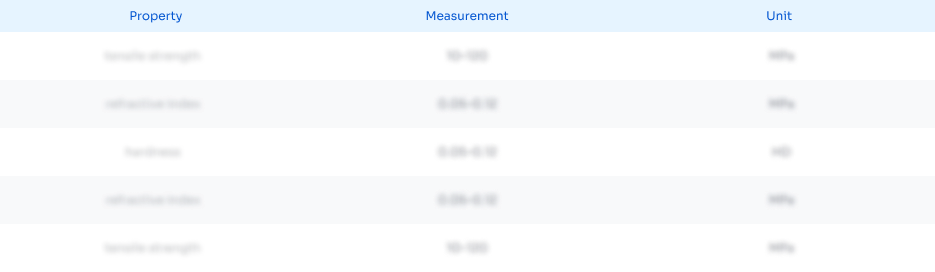
Abstract
Description
Claims
Application Information

- Generate Ideas
- Intellectual Property
- Life Sciences
- Materials
- Tech Scout
- Unparalleled Data Quality
- Higher Quality Content
- 60% Fewer Hallucinations
Browse by: Latest US Patents, China's latest patents, Technical Efficacy Thesaurus, Application Domain, Technology Topic, Popular Technical Reports.
© 2025 PatSnap. All rights reserved.Legal|Privacy policy|Modern Slavery Act Transparency Statement|Sitemap|About US| Contact US: help@patsnap.com