Preparing method for porous Fe-Si-C ceramic micro balls
A technology of ceramic microspheres and fe-si-c, which is applied in the field of preparation of porous Fe-Si-C ceramic microspheres obtained by cracking, can solve the problem that Fe-Si-C ceramic microspheres have not been reported and the preparation of SiC ceramic microspheres The method is limited and other problems, to achieve the effect of being suitable for large-scale production, narrow particle size distribution, and good stability
- Summary
- Abstract
- Description
- Claims
- Application Information
AI Technical Summary
Problems solved by technology
Method used
Image
Examples
reference example 1
[0036] Reference example 1: the preparation of ferrocene lithium salt:
[0037]Vacuumize the synthesis reaction system, replace high-purity nitrogen to normal pressure, repeat 3 times; add 10 g (53.8 mmol) ferrocene and 70 mL of anhydrous n-hexane solvent into a dry 250 mL reaction bottle, stir; then add 10 mL (66.7 mmol) of tetramethylethylenediamine; after stirring evenly, add 53 mL of n-hexane solution with a molar concentration of n-butyllithium of 2.4 mol / L dropwise, stir, and react for 10 h; filter under reduced pressure, remove the filtrate, Adopt anhydrous n-hexane to wash the orange-red solid filter residue 3 times, and vacuum-dry to remove the n-hexane in the filter residue to obtain 13.3 g ferrocene lithium salt (Fe(η-C 5 h 4 Li 2 )·2 / 3TMEDA). The dried lithium ferrocene salt was stored in an argon-protected glove box.
reference example 2
[0038] Reference example 2: Synthesis of polyferrocenyl silane:
[0039] Vacuumize the synthesis reaction system, replace high-purity nitrogen to normal pressure, repeat 3 times, take 5 g (18.2 mmol) of ferrocene lithium salt prepared in Reference Example 1 in a 250 mL reaction bottle in the glove box, seal it well Remove and place in a -20°C reaction bath, inject 50 mL of anhydrous tetrahydrofuran (THF) with a syringe, stir to dissolve; then add Cl dropwise through a constant pressure dropping funnel 2 Si(CH 3 ) 2 solution in THF (0.94 g (7.3 mmol) Cl 2 Si(CH 3 ) 2 Dissolved in 30 mL THF), stirred at -20°C for 1 h; then added Cl dropwise through a constant pressure dropping funnel 3 SiCH 3 solution in THF (1.09 g (7.3 mmol) Cl 3 Si CH 3 dissolved in 30 mL THF), stirred at 25°C for 12 hours; finally, 1 mL of methanol was added dropwise to terminate the reaction, filtered, the filtrate was concentrated to 20 mL, the concentrated solution was added dropwise to the stir...
Embodiment 1
[0041] (1) Dissolve 0.3 g PFS in 2.7 mL of an organic solvent (a solvent mixed with tetrahydrofuran and xylene at a volume ratio of 2:1), stir, and prepare a 3 mL polymer solution with a mass fraction of 10 wt %, and stir to obtain a composite Part a; (2) Dissolve 20 g of gelatin in 180 mL of deionized water at 80°C, stir to form 200 mL of gelatin emulsion with a mass fraction of 10wt%, and obtain component b; (3) At 60°C, stir at a speed of 300 At r / min, drop the component a obtained in step (1) into the component b obtained in step (2) with a rubber dropper, micro-droplets appear, continue to stir for 4 h, let stand, and the polymer microspheres sink in At the bottom, pour the upper emulsion, add 1L of deionized water, dilute the gelatin emulsion containing polymer microspheres, filter, collect the microspheres, then wash the microspheres with deionized water for 3 times, wash with ethanol for 2 times, and finally at 55 °C, Vacuum-dried for 8 h to obtain polymer microspheres...
PUM
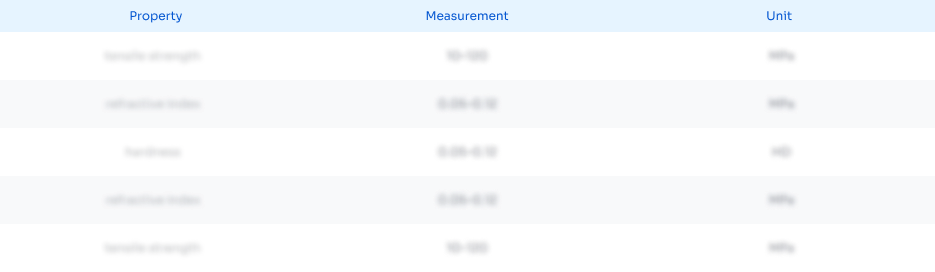
Abstract
Description
Claims
Application Information

- R&D
- Intellectual Property
- Life Sciences
- Materials
- Tech Scout
- Unparalleled Data Quality
- Higher Quality Content
- 60% Fewer Hallucinations
Browse by: Latest US Patents, China's latest patents, Technical Efficacy Thesaurus, Application Domain, Technology Topic, Popular Technical Reports.
© 2025 PatSnap. All rights reserved.Legal|Privacy policy|Modern Slavery Act Transparency Statement|Sitemap|About US| Contact US: help@patsnap.com