De-silicication purifying method for fluorite for pre-melted slag
A purification method and pre-melted slag technology, which is applied in the field of fluorite purification, can solve the problems of low environmental protection, complicated process and high cost, and achieve the effect of improving grade, simple process and promoting development
- Summary
- Abstract
- Description
- Claims
- Application Information
AI Technical Summary
Problems solved by technology
Method used
Image
Examples
Embodiment 1
[0029] Crush 200 kilograms of fluorite to 100 mesh, and leaching it with hydrofluoric acid with a concentration of 1.5mol / L in a 2000L reaction tank at a solid-to-liquid ratio (kg:liter) of 1:2.0. The leaching time is 9 hours. Obtain leaching solution, leaching slag and exhaust gas; rinse the leaching slag with deionized water with a water pressure of 0.5MPa for 10 minutes, and then dry it to obtain the final fluorite product; the exhaust gas is filled with 4000L of hydrogen with a concentration of 4.5mol / L 9m of sodium oxide solution 3 In the exhaust gas collection tank, carry out harmless treatment; add 168L of deionized water and 33L of industrial grade hydrofluoric acid solution containing 40wt% hydrogen fluoride to the leaching solution, and prepare the hydrofluoric acid with a concentration of 2.0mol / L for the next batch of fluorite to process. The percentages of chemical components of fluorite before and after treatment are shown in Table 1.
[0030] Product analysis ...
Embodiment 2
[0033] Crush 200 kg of fluorite to 150 mesh, and leaching it with hydrofluoric acid with a concentration of 2.0 mol / L in a 2000L reaction tank at a solid-to-liquid ratio (kg: liter) of 1:3.0. The leaching time is 10 hours. Obtain leaching liquid, leaching slag and exhaust gas; rinse the leaching slag with deionized water with a water pressure of 0.8MPa for 16 minutes, and then dry it to obtain the final fluorite product; the exhaust gas is filled with 4000L of hydrogen with a concentration of 4.4mol / L 9m of sodium oxide solution 3 In the exhaust gas collection tank, carry out harmless treatment; add 143L of deionized water and 59L of industrial-grade hydrofluoric acid solution containing 40wt% hydrogen fluoride to the leachate, and prepare the hydrofluoric acid with a concentration of 3.0mol / L for the next batch of fluorite to process. The percentages of chemical components of fluorite before and after treatment are shown in Table 2.
[0034] Product analysis result (wt%) in...
Embodiment 3
[0037] Crush 200 kg of fluorite to 200 mesh, and leaching it with hydrofluoric acid with a concentration of 3.0 mol / L in a 2000L reaction tank at a solid-to-liquid ratio (kg: liter) of 1:4.0. The leaching time is 12 hours. Obtain leaching solution, leaching slag and exhaust gas; rinse the leaching slag with deionized water with a water pressure of 1.2MPa for 14 minutes, and then dry to obtain the final fluorspar product; the exhaust gas is passed into a 4000L container with an initial concentration of 4.5mol / L 9m of sodium hydroxide solution 3 In the exhaust gas collection tank, carry out harmless treatment; add 2L of industrial grade hydrofluoric acid solution containing 40wt% hydrogen fluoride to the leachate, and prepare hydrofluoric acid with a concentration of 2.8mol / L to treat the next batch of fluorite; The percentages of chemical components of fluorite before and after treatment are shown in Table 3. After the sodium hydroxide solution in the waste gas collection tank...
PUM
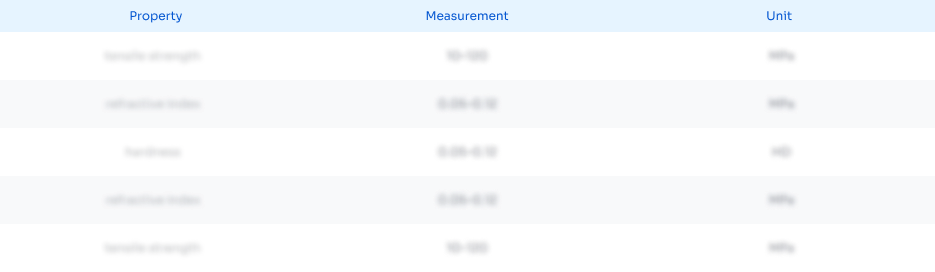
Abstract
Description
Claims
Application Information

- Generate Ideas
- Intellectual Property
- Life Sciences
- Materials
- Tech Scout
- Unparalleled Data Quality
- Higher Quality Content
- 60% Fewer Hallucinations
Browse by: Latest US Patents, China's latest patents, Technical Efficacy Thesaurus, Application Domain, Technology Topic, Popular Technical Reports.
© 2025 PatSnap. All rights reserved.Legal|Privacy policy|Modern Slavery Act Transparency Statement|Sitemap|About US| Contact US: help@patsnap.com