Expansion-type fireproof paint used for lost foam
A fire retardant coating, intumescent technology, applied in the direction of coating, mold, core, etc., can solve the problems of sticking sand, difficult to remove, etc., and achieve the effect of improving fire resistance limit and excellent stability
- Summary
- Abstract
- Description
- Claims
- Application Information
AI Technical Summary
Problems solved by technology
Method used
Examples
Embodiment 1
[0014] An intumescent fireproof coating for lost foam is characterized in that the components of the raw materials are composed as follows according to parts by weight:
[0015] Acrylic resin, urea-formaldehyde resin, and phenol-formaldehyde epoxy resin are composed of 35 parts of composite resin according to the weight ratio of 3:2:1, 8 parts of n-butyl acetate, 6 parts of ammonium polyphosphate, 4 parts of chlorinated terphenyl, and 3 parts of glass wool 1.2 parts, 0.6 parts of potassium ammonium polyphosphate, 2 parts of nano-magnesium hydroxide, 1.2 parts of char-forming agent composed of sorbitol and pentaerythritol according to the molar ratio of 1:2, 3 parts of hydroxyethyl cellulose, and 0.5 parts of sodium fluorosilicate.
Embodiment 2
[0017] An intumescent fireproof coating for lost foam is characterized in that the components of the raw materials are composed as follows according to parts by weight:
[0018] Acrylic resin, urea-formaldehyde resin, and phenol-formaldehyde epoxy resin are composed of 340 parts of composite resin in a weight ratio of 3:2:1, 10 parts of n-butyl acetate, 8 parts of ammonium polyphosphate, 5 parts of chlorinated terphenyl, and 4 parts of glass wool 1.3 parts, 0.7 parts of potassium ammonium polyphosphate, 3 parts of nano-magnesium hydroxide, 1.3 parts of char-forming agent composed of sorbitol and pentaerythritol according to the molar ratio of 1:2, 4 parts of hydroxyethyl cellulose, and 0.6 parts of sodium fluorosilicate.
Embodiment 3
[0020] An intumescent fireproof coating for lost foam is characterized in that the components of the raw materials are composed as follows according to parts by weight:
[0021] Acrylic resin, urea-formaldehyde resin, and phenol-formaldehyde epoxy resin are composed of 45 parts of composite resin in a weight ratio of 3:2:1, 12 parts of n-butyl acetate, 9 parts of ammonium polyphosphate, 6 parts of chlorinated terphenyl, and 5 parts of glass wool 1.5 parts, 0.8 parts of potassium ammonium polyphosphate, 4 parts of nano-magnesium hydroxide, 1.5 parts of char-forming agent composed of sorbitol and pentaerythritol according to the molar ratio of 1:2, 5 parts of hydroxyethyl cellulose, and 0.7 parts of sodium fluorosilicate.
PUM
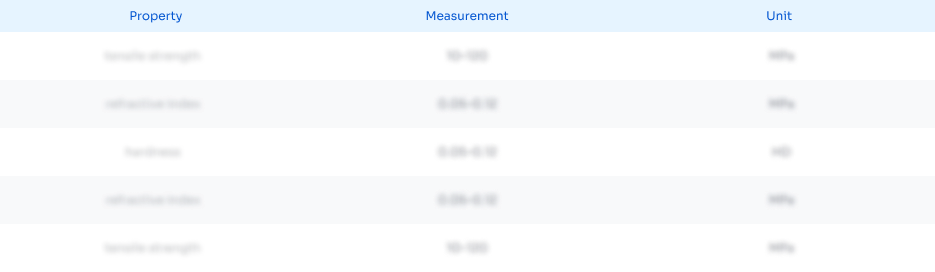
Abstract
Description
Claims
Application Information

- R&D
- Intellectual Property
- Life Sciences
- Materials
- Tech Scout
- Unparalleled Data Quality
- Higher Quality Content
- 60% Fewer Hallucinations
Browse by: Latest US Patents, China's latest patents, Technical Efficacy Thesaurus, Application Domain, Technology Topic, Popular Technical Reports.
© 2025 PatSnap. All rights reserved.Legal|Privacy policy|Modern Slavery Act Transparency Statement|Sitemap|About US| Contact US: help@patsnap.com