A kind of production method of crease-free synthetic leather
A production method and technology for synthetic leather, applied in the field of synthetic leather, can solve the problems of increasing cost, reducing the softness and comfort performance of synthetic leather, increasing the hardness of synthetic leather, etc. The effect of good folding resistance
- Summary
- Abstract
- Description
- Claims
- Application Information
AI Technical Summary
Problems solved by technology
Method used
Image
Examples
Embodiment 1
[0031] Table 1.1 Formula of modified polyamide resin
[0032] material composition
weight
polyamide resin
100kg
Organic Montmorillonite
5kg
Antioxidant (tetraerythritol ester)
0.35kg
[0033] Table 1.2 Impregnation formula:
[0034]
[0035]
[0036] Table 1.3 Weight formula of adhesive layer polyurethane compounding liquid:
[0037]
[0038] First, prepare the corresponding materials according to the formulations in Tables 1.1 to 1.3, and the polyurethane solution with a solid content greater than 65%.
[0039] Further, the first material component is blended through a twin-screw extruder to realize melt intercalation and granulation. The processing temperature of this process is 75°C to 125°C; through this step, the modified polyamide resin is obtained .
[0040] Further, 100 kg of the modified polyamide resin and 30 kg of polyamide resin formed above are prepared for blend spinning, and the base fabric is formed...
Embodiment 2
[0049] Table 2.1 Formula of modified polyamide resin
[0050] material composition
weight
polyamide resin
100kg
Organic Montmorillonite
8kg
0.6kg
[0051] Table 2.2 Impregnation formula:
[0052]
[0053]
[0054] Table 2.3 Weight formula of polyurethane compounding liquid for adhesive layer:
[0055]
[0056] First, prepare the corresponding materials according to the formulations in Table 2.1 to 2.3, and the polyurethane solution with a solid content greater than 65%.
[0057] Further, the first material component is blended through a twin-screw extruder to realize melt intercalation and granulation. The processing temperature of this process is 75°C to 125°C; through this step, the modified polyamide resin is obtained .
[0058] Further, 100 kg of modified polyamide resin and 26 kg of polyamide resin formed above are prepared for blend spinning, and the base fabric is formed by traditional techniques...
Embodiment 3
[0067] Table 3.1 Modified polyamide resin formula
[0068] material composition
weight
polyamide resin
80kg
Organic Montmorillonite
1kg
0.2kg
[0069] Table 3.2 Impregnation formula:
[0070]
[0071]
[0072] Table 3.3 Weight formula of polyurethane compounding liquid for adhesive layer:
[0073]
[0074] First, prepare the corresponding materials according to the formulations in Table 3.1 to 3.3, and the polyurethane solution with a solid content greater than 65%.
[0075] Further, the first material component is blended by a twin-screw extruder to realize melt intercalation and granulation, and the processing temperature of this process is 75° C.; through this step, a modified polyamide resin is obtained.
[0076] Further, 100 kg of the modified polyamide resin and 25 kg of polyamide resin formed above are prepared for blend spinning, and the base fabric is formed by traditional techniques such as tex...
PUM
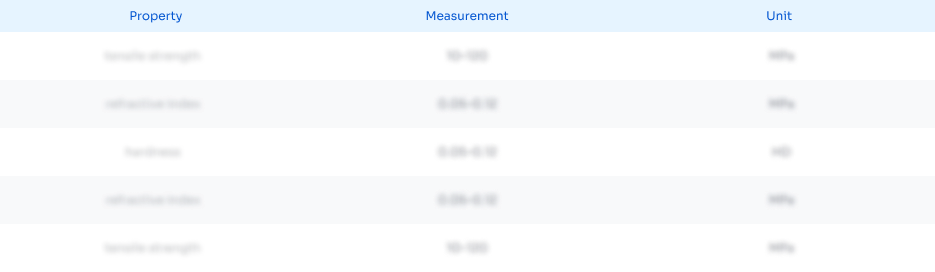
Abstract
Description
Claims
Application Information

- R&D
- Intellectual Property
- Life Sciences
- Materials
- Tech Scout
- Unparalleled Data Quality
- Higher Quality Content
- 60% Fewer Hallucinations
Browse by: Latest US Patents, China's latest patents, Technical Efficacy Thesaurus, Application Domain, Technology Topic, Popular Technical Reports.
© 2025 PatSnap. All rights reserved.Legal|Privacy policy|Modern Slavery Act Transparency Statement|Sitemap|About US| Contact US: help@patsnap.com