Clean production method for separating manganese and magnesium from laterite-nickel ore normal-temperature acid leaching liquid employing alkaline oxidation
A technology of laterite nickel ore and alkaline oxidation is applied in the direction of improving process efficiency, which can solve the problems of expensive precipitating agent and environmental damage, and achieve the effects of low price, realizing recycling and improving comprehensive utilization rate.
- Summary
- Abstract
- Description
- Claims
- Application Information
AI Technical Summary
Problems solved by technology
Method used
Image
Examples
Embodiment 1
[0030] The Ni, Co, Mn and Mg contents are respectively 2.36g / L, 0.165g / L, 0.83g / L and 14.47g / L laterite nickel ore normal pressure acid leaching solution mixed with 5wt.% NaOH solution to adjust the solution The pH is 9, while adding 30wt.% of H 2 o 2 The solution was reacted at 20°C for 1 hour, and the reacted solution was subjected to liquid-solid separation, and the filtrate mainly contained a large amount of Mg 2+ , Ni 2+ 、Co 2+ and Mn 2+ Mainly precipitated as Ni(OH) 2 、Co(OH) 2 and MnO 2 ; The obtained slag and 10wt.% HCl are controlled at room temperature (20° C.) to have a pH of 1, and the reaction is performed for 1 h. At this time, Ni(OH) 2 、Co(OH) 2 dissolved, MnO 2 Undissolved, filtered, residue MnO 2Carry out oven dry (120 ℃), purity requirement can satisfy industrial application; At this moment, the rate of recovery of Ni, Co, Mn and Mg is respectively 97.1%, 90.2%, 92.7% and 99.8%; % NaOH, 30wt.% H 2 o 2 , the temperature is 20°C, the pH is 9, and t...
Embodiment 2
[0032] The Ni, Co, Mn and Mg contents are respectively 2.35g / L, 0.17g / L, 0.93g / L and 15.13g / L of laterite nickel ore normal pressure acid leaching solution mixed with 10wt.% NaOH solution to adjust the solution The pH is 7.5, while adding 5wt.% of H 2 o 2 The solution was reacted at a temperature of 50°C for 1.5 hours, and the reacted solution was subjected to liquid-solid separation, and the filtrate mainly contained a large amount of Mg 2+ , Ni 2+ 、Co 2+ and Mn 2+ Mainly precipitated as Ni(OH) 2 、Co(OH) 2 and MnO 2 ; The resulting slag and 15wt.% of HCl are controlled at room temperature (20°C) to have a pH of 3, and react for 0.5h. At this time, Ni(OH) 2 、Co(OH) 2 dissolved, MnO 2 Undissolved, filtered, residue MnO 2 Carry out oven dry (80 ℃), purity requirement can meet industrial application; At this moment, the rate of recovery of Ni, Co, Mn and Mg is respectively 98.5%, 91.2%, 93.1% and 98.9%; % NaOH, 10wt.% H 2 o 2 , the temperature is 50°C, the pH is 7.5,...
Embodiment 3
[0034] The Ni, Co, Mn and Mg contents are respectively 2.30g / L, 0.16g / L, 0.84g / L and 14.41g / L laterite nickel ore normal pressure acid leaching solution mixed with 55wt.% NaOH solution to adjust the solution The pH is 10, while adding 20wt.% of H 2 o 2 The solution was reacted at a temperature of 50°C for 0.5h, and the reacted solution was subjected to liquid-solid separation, and the filtrate mainly contained a large amount of Mg 2+ , Ni 2+ 、Co 2+ and Mn 2+ Mainly precipitated as Ni(OH) 2 、Co(OH) 2 and MnO 2 ; The obtained slag and 2.5wt.% HCl are controlled at 50°C to have a pH of 0.5, and react for 3 hours, at which point Ni(OH) 2 、Co(OH) 2 dissolved, MnO 2 Undissolved, filtered, residue MnO 2 Carry out oven dry (100 ℃), purity requirement can satisfy industrial application; At this moment, the rate of recovery of Ni, Co, Mn and Mg is respectively 96.8%, 90.5%, 91.7% and 95.3%; % NaOH, 20wt.% H 2 o 2 , the temperature is 50°C, the pH is 10, and the reaction is ...
PUM
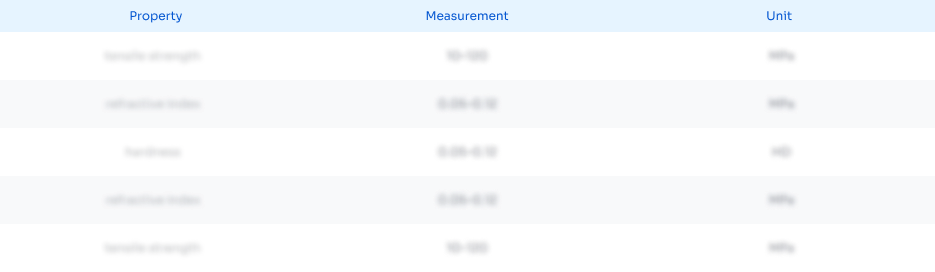
Abstract
Description
Claims
Application Information

- R&D
- Intellectual Property
- Life Sciences
- Materials
- Tech Scout
- Unparalleled Data Quality
- Higher Quality Content
- 60% Fewer Hallucinations
Browse by: Latest US Patents, China's latest patents, Technical Efficacy Thesaurus, Application Domain, Technology Topic, Popular Technical Reports.
© 2025 PatSnap. All rights reserved.Legal|Privacy policy|Modern Slavery Act Transparency Statement|Sitemap|About US| Contact US: help@patsnap.com