Method for machining lens cone part with mass center deviating from rotation center
A turning center and parts processing technology, applied in the field of mechanical processing, can solve the problems affecting the production cycle, difficult to guarantee geometric tolerances such as cylindricity and coaxiality of holes, and low product qualification rate, so as to achieve small vibration and improve processing accuracy and production efficiency, simple operation effect
- Summary
- Abstract
- Description
- Claims
- Application Information
AI Technical Summary
Problems solved by technology
Method used
Examples
Embodiment Construction
[0016] The method for processing the lens barrel parts whose center of mass deviates from the center of rotation of the present invention comprises the following steps:
[0017] The first step is to cast the blank;
[0018] The second step, heat treatment, adopts quenching aging treatment;
[0019] In the third step, the fitter draws the distribution line of the blank allowance based on the non-processing surface;
[0020] Step 4: On the milling machine, mill each surface of the installation base, and leave a finishing allowance of 0.1 mm on the lower end of the ruler;
[0021] The fifth step is to rough each hole on the lathe, and reserve 0.5mm margin for one side of the finishing surface;
[0022] The sixth step, heat treatment, heat treatment for stress relief artificial aging, eliminate processing stress;
[0023] The seventh step is to process the fine reference mounting surface, that is, the flatness of the lower end surface scraped by the fitter is within 0.006 mm, ...
PUM
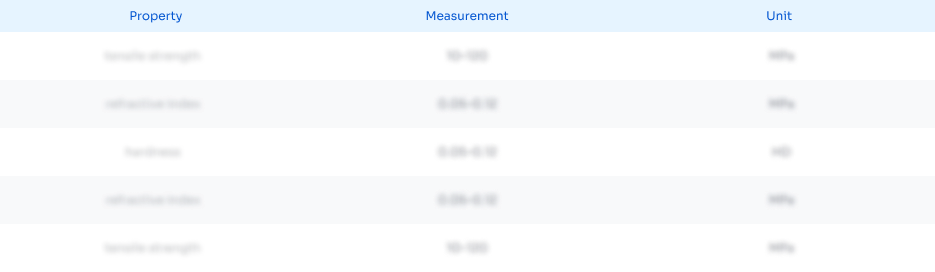
Abstract
Description
Claims
Application Information

- R&D Engineer
- R&D Manager
- IP Professional
- Industry Leading Data Capabilities
- Powerful AI technology
- Patent DNA Extraction
Browse by: Latest US Patents, China's latest patents, Technical Efficacy Thesaurus, Application Domain, Technology Topic, Popular Technical Reports.
© 2024 PatSnap. All rights reserved.Legal|Privacy policy|Modern Slavery Act Transparency Statement|Sitemap|About US| Contact US: help@patsnap.com