Epoxy resin self-repairing microcapsule and preparation method thereof
A self-healing microcapsule, epoxy resin technology, applied in the field of composite materials, can solve the problems of unevenness, weakened catalytic efficiency, large size, etc., and achieves simple process, excellent stability and tightness, and little influence on the mechanical properties of the matrix. Effect
- Summary
- Abstract
- Description
- Claims
- Application Information
AI Technical Summary
Problems solved by technology
Method used
Image
Examples
Embodiment 1
[0044] Add 0.5 g of hectorite particles (purchased from Rockwood, with an average particle size of 105 nm, a maximum particle size of 500 nm, and a minimum particle size of 20 nm) into 100 g of water to obtain a dispersion as the water phase. Mix 1.0g of bisphenol A type epoxy resin E51 (purchased from Bluestar New Material Company), 0.5g of oil-soluble monomer styrene (St), 0.5g of oil-soluble crosslinking agent divinylbenzene (DVB), 0.5g Styrene and 0.002 g of initiator azobisisobutyronitrile (AIBN) were mixed, and the mixed liquid was used as an oil phase. Put the water phase and the oil phase into a 70°C oven to heat for 20 minutes and 3 minutes respectively for preheating, and stir to mix the components of the oil phase evenly (the total mass of epoxy resin E51 and monomer and crosslinking agent The mass ratio is 1:1, the mass ratio of divinylbenzene to styrene is 1:1). The water phase and the oil phase are mixed, and a stable oil-in-water emulsion is obtained by high-sp...
Embodiment 2
[0050] An aqueous solution of 0.5 g of silicon carbide particles (purchased from Sinopharm Chemical Reagent Co., Ltd., with an average particle size of 80 nm, a minimum particle size of 5 nm, and a maximum particle size of 230 nm) and 0.2 g of potassium persulfate (1% KPS) was added to 100 g In water, a dispersion was obtained as an aqueous phase. Mix 0.1g oil-soluble crosslinking agent ethylene glycol di(methacrylate) ester (EGDMA), 0.1g oil-soluble monomer methyl methacrylate (MMA), and 1.0g bisphenol A epoxy resin E51, This mixed solution was used as the oil phase. Put the water phase and the oil phase into a 70°C oven to heat for 20 minutes and 3 minutes respectively for preheating, and stir to mix the components of the oil phase evenly (the total mass of epoxy resin E51 and monomer and crosslinking agent The mass ratio is 5:1, and the mass ratio of methyl methacrylate to ethylene glycol di(methacrylate) ester is 1:1). The water phase and the oil phase are mixed, and a s...
Embodiment 3
[0055] Add 0.5 g of lithium diatomaceous earth particles (purchased from Rockwood (Rockwood) company, with an average particle size of 105 nm, a maximum particle size of 500 nm, and a minimum particle size of 20 nm) and 0.2 g of initiator azobisisobutyronitrile (AIBN) into the 100 g of water to obtain a dispersion as an aqueous phase. Mix 1.0g bisphenol A type epoxy resin F44 (purchased from Blue Star New Material Company) from Shanghai Resin Factory, 0.1g oil-soluble crosslinking agent divinylbenzene (DVB) and 0.1g styrene (St), This mixed solution was used as an oil phase. Put the water phase and the oil phase into a 70°C oven to heat for 20 minutes and 5 minutes respectively for preheating, and stir to mix the components of the oil phase evenly (wherein the mass ratio of epoxy resin F44 to the total mass of monomers is 5: 1. The mass ratio of divinylbenzene to styrene is 1:1). The water phase and oil phase prepared above were mixed, and the temperature was raised to 70° C...
PUM
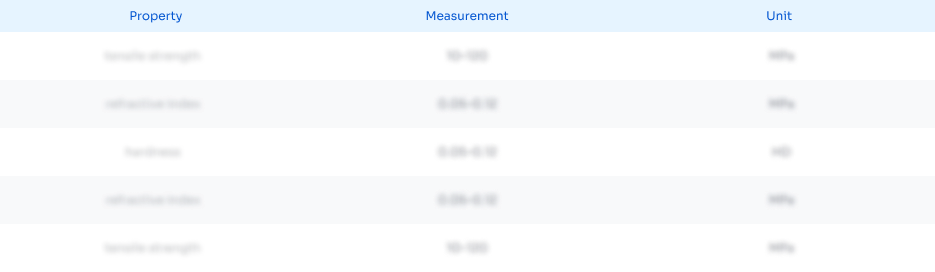
Abstract
Description
Claims
Application Information

- R&D
- Intellectual Property
- Life Sciences
- Materials
- Tech Scout
- Unparalleled Data Quality
- Higher Quality Content
- 60% Fewer Hallucinations
Browse by: Latest US Patents, China's latest patents, Technical Efficacy Thesaurus, Application Domain, Technology Topic, Popular Technical Reports.
© 2025 PatSnap. All rights reserved.Legal|Privacy policy|Modern Slavery Act Transparency Statement|Sitemap|About US| Contact US: help@patsnap.com