Working roll forming technology taking grinding precision and cold-rolled electrical steel edge drop control into consideration
A technology for work rolls and electrical steel, applied in the direction of rolls, metal rolling, metal rolling, etc., which can solve the problem of few adjustable parameters of roll shape curves, low roll grinding accuracy and efficiency, and no consideration of edge drop control for work rolls Grinding accuracy and efficiency and other issues
- Summary
- Abstract
- Description
- Claims
- Application Information
AI Technical Summary
Problems solved by technology
Method used
Image
Examples
Embodiment Construction
[0038] Below in conjunction with specific implementation case the present invention will be further described:
[0039] For a 1720mm electrical steel cold tandem rolling unit in a factory, the work rolls of this unit have no roll shifting function, and there are a large number of 1000mm width electrical steel products in production, because the length of the roll surface is much larger than the width of the strip. Therefore, the side drop control effect is not good when the conventional side drop control taper work roll is used, and because the tapered section is very long, the partial wear of the grinding wheel is serious during the grinding of the work roll, resulting in a significant increase in the grinding accuracy and grinding efficiency of the side drop work roll. Decline, sometimes repeated grinding phenomenon.
[0040] According to the content of the present invention, the corresponding work roll profile curve is designed. According to the field measurement results, ...
PUM
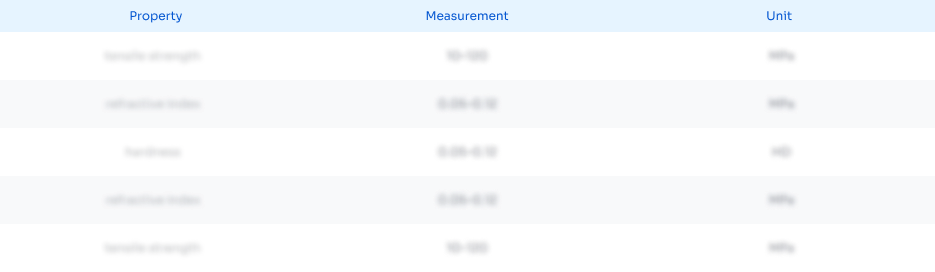
Abstract
Description
Claims
Application Information

- R&D
- Intellectual Property
- Life Sciences
- Materials
- Tech Scout
- Unparalleled Data Quality
- Higher Quality Content
- 60% Fewer Hallucinations
Browse by: Latest US Patents, China's latest patents, Technical Efficacy Thesaurus, Application Domain, Technology Topic, Popular Technical Reports.
© 2025 PatSnap. All rights reserved.Legal|Privacy policy|Modern Slavery Act Transparency Statement|Sitemap|About US| Contact US: help@patsnap.com