Two-degree-of-freedom piezoelectric driving nanometer positioning platform
A nano-positioning and piezoelectric drive technology, applied in the direction of machines/supports, supporting machines, mechanical equipment, etc., can solve the problems of small load bearing capacity, difficult to reach the stroke, low driving power, etc., to prevent breakdown and reduce The effect of motion cross-coupling and high space utilization
- Summary
- Abstract
- Description
- Claims
- Application Information
AI Technical Summary
Problems solved by technology
Method used
Image
Examples
Embodiment Construction
[0040] Below in conjunction with accompanying drawing and embodiment the present invention will be further described:
[0041] like figure 1 and figure 2 As shown, the present invention is a micro-movement nano-shift positioning platform driven by a piezoelectric ceramic driver and decoupled in parallel in the XY direction, including a base 1, an L-shaped symmetrical amplifying lever 2, and a composite parallel four-bar guide mechanism 3 , Cross-shaped XY decoupling mechanism 4, XY motion platform body 5, piezoelectric ceramic driver 6, laser ruler plane mirror and mirror frame 7.
[0042] The XY motion platform body 5 and the base 1 pass through the fully compliant mechanism in the X-axis direction, the fully compliant mechanism in the Y-axis direction, the first cross-shaped XY decoupling mechanism 41 with four-corner symmetry, and the second cross-shaped XY decoupling mechanism 42 , the third cross-shaped XY decoupling mechanism 43 and the fourth cross-shaped XY decoupli...
PUM
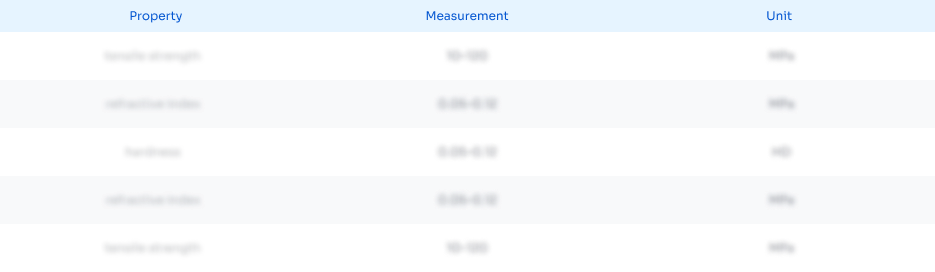
Abstract
Description
Claims
Application Information

- R&D Engineer
- R&D Manager
- IP Professional
- Industry Leading Data Capabilities
- Powerful AI technology
- Patent DNA Extraction
Browse by: Latest US Patents, China's latest patents, Technical Efficacy Thesaurus, Application Domain, Technology Topic, Popular Technical Reports.
© 2024 PatSnap. All rights reserved.Legal|Privacy policy|Modern Slavery Act Transparency Statement|Sitemap|About US| Contact US: help@patsnap.com