Method for microwave pre-roasting and submerged arc furnace combined production of manganese-iron alloy
A technology of ferromanganese alloy and joint production is applied in the field of microwave pre-roasting and submerged arc furnace joint production of ferromanganese alloy, which can solve the problems of large load of smelting furnace, low productivity, easy material collapse, etc., and achieves improved productivity and fast heating rate. , to avoid the effect of collapse
- Summary
- Abstract
- Description
- Claims
- Application Information
AI Technical Summary
Problems solved by technology
Method used
Image
Examples
Embodiment 1
[0028] The method for producing ferromanganese alloy in conjunction with microwave pre-roasting and submerged arc furnace, its specific steps are as follows:
[0029] Step 1. First, crush manganese ore and carbonaceous reducing agent to a particle size of 5-30mm and 1-20mm, and then mix the crushed manganese ore and carbonaceous reducing agent uniformly according to the mass ratio of 65:35 to obtain a mixed material; wherein Manganese ore includes the following mass percentage components: Mn 2 o 3 35.21%, Fe 3 o 4 5.6%, CaCO 3 25%; carbonaceous reducing agent is petroleum coke;
[0030] Step 2. Heat the mixed material obtained in step 1 to 750°C for 50 minutes under microwave conditions to obtain a hot material with no sintering and low pulverization rate maintained at 721°C. The hot material has no moisture and carbonic acid Salt decomposition rate and high-valent manganese oxide reduction rate reached 71%;
[0031] Step 3. Then put the hot material obtained in step 2 i...
Embodiment 2
[0033] Such as figure 1 Shown, this microwave pre-roasting and submerged arc furnace are combined to produce the method for ferromanganese alloy, and its concrete steps are as follows:
[0034] Step 1, first crushing manganese ore and carbonaceous reducing agent to a particle size of 5-50mm, 1-10mm, and then mixing the crushed manganese ore and carbonaceous reducing agent according to the mass ratio of 70:30 to obtain a mixed material; wherein Manganese ore includes the following mass percentage components: Mn 2 o 3 44.51%, Fe 3 o 4 7.43%, CaCO 3 24.54%; carbonaceous reducing agent is coke;
[0035] Step 2. Heat the mixed material obtained in step 1 to 850°C for 40 minutes under microwave conditions to obtain a hot material with no sintering and low pulverization rate maintained at 821°C. The hot material has no moisture and carbonic acid The salt decomposition rate and the high-valent manganese oxide reduction rate reach 81%; the microwave pre-roasting process is carrie...
Embodiment 3
[0038] Such as figure 1 Shown, this microwave pre-roasting and submerged arc furnace are combined to produce the method for ferromanganese alloy, and its concrete steps are as follows:
[0039]Step 1. First, crush the manganese ore and carbonaceous reducing agent to a particle size of 5-80mm and 1-30mm, and then mix the crushed manganese ore and carbonaceous reducing agent uniformly according to the mass ratio of 72:28 to obtain a mixed material; wherein Manganese ore includes the following mass percentage components: Mn 2 o 3 37.19%, Fe 3 o 4 6.32%, CaCO 3 26.42%; carbonaceous reducing agent is coal;
[0040] Step 2. Heat the mixed material obtained in step 1 to 900°C for 25 minutes under microwave conditions to obtain a hot material with no sintering and low pulverization rate maintained at 821°C. The hot material has no moisture and carbonic acid The salt decomposition rate and the high-valent manganese oxide reduction rate reach 81%; the microwave pre-roasting proces...
PUM
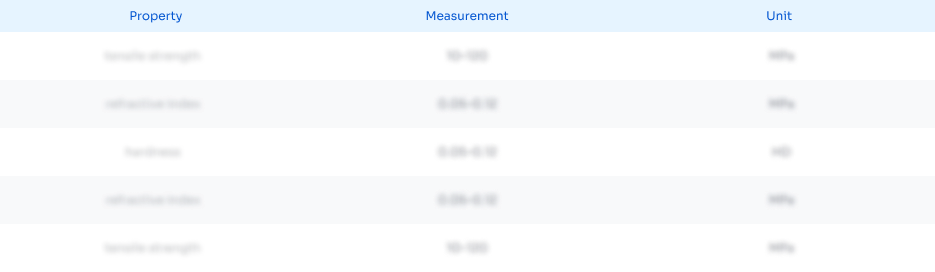
Abstract
Description
Claims
Application Information

- R&D
- Intellectual Property
- Life Sciences
- Materials
- Tech Scout
- Unparalleled Data Quality
- Higher Quality Content
- 60% Fewer Hallucinations
Browse by: Latest US Patents, China's latest patents, Technical Efficacy Thesaurus, Application Domain, Technology Topic, Popular Technical Reports.
© 2025 PatSnap. All rights reserved.Legal|Privacy policy|Modern Slavery Act Transparency Statement|Sitemap|About US| Contact US: help@patsnap.com