Halogen lamp producing technique
A manufacturing process, a halogen lamp technology, applied in the direction of electrical components, etc., can solve the problems of tungsten wire atomic arrangement is not tight, oxide impurities are difficult to remove, and the structure is not stable enough, so as to improve the service life and lumens, increase the number of lumens , the effect of reducing hair
- Summary
- Abstract
- Description
- Claims
- Application Information
AI Technical Summary
Problems solved by technology
Method used
Image
Examples
Embodiment 1
[0030] The process is divided into five steps. First, (1) Blister manufacturing: the steps are feeding, rough sawing, storage, fine sawing, cleaning, drying and taking over. The raw materials of the feeding process are quartz tubes, rough sawing tubes The process is divided into three steps: adjustment of position, sawing and inspection. The tool used in the sawing process is a grinder. In the cleaning process, 50ml of distilled water is used to clean 3 times. In the drying process, the temperature is first heated to 40°C and kept for 20 minutes. Reheat to 90°C and keep it for 40 minutes. The takeover process is divided into five steps: melting port, flaring, softening and drawing, taking over cooling and singeing. Adjust the temperature to 3200°C, and then carry out (2) Filament manufacturing: the steps are raw material treatment, primary winding, chemical degreasing, primary setting, secondary winding, chemical degreasing, secondary wet hydrogen setting, shredding, burning H...
Embodiment 2
[0032] Repeat Example 1 according to the same steps described above, the difference is that in the cleaning process in step (1), use 65ml of distilled water to wash 4 times, and in the drying process, first heat the temperature to 45°C, keep it for 25 minutes, and then heat to 95°C and keep it for 45 minutes, heat up to 3550°C in the melting port process, adjust the temperature to 3250°C in the softening and drawing process, and adjust the temperature to 3250°C in the step (2), raise the temperature to 3450°C in the spinning process, and chemically degrease In the process, a sodium bicarbonate solution with a concentration of 25% is used in step (4), and the pressure is adjusted to 1.25×10^6-5Pa in the high-pressure treatment process, and kept for 9 hours.
Embodiment 3
[0034] Repeat Example 1 according to the same steps described above, the difference is: in the cleaning process in step (1), use 80ml of distilled water to wash 5 times, and in the drying process, first heat the temperature to 50 ° C, keep it for 30 minutes, and then heat to 100°C and keep it for 50 minutes, heat up to 3600°C in the melting port process, adjust the temperature to 3300°C in the softening and drawing process, and adjust the temperature to 3300°C in the step (2), raise the temperature to 3500°C in the spinning process, and chemically degrease A sodium bicarbonate solution with a concentration of 30% is used in the process. In step (4), the pressure is adjusted to 1.3×10^6Pa in the high pressure treatment process and kept for 10 hours.
PUM
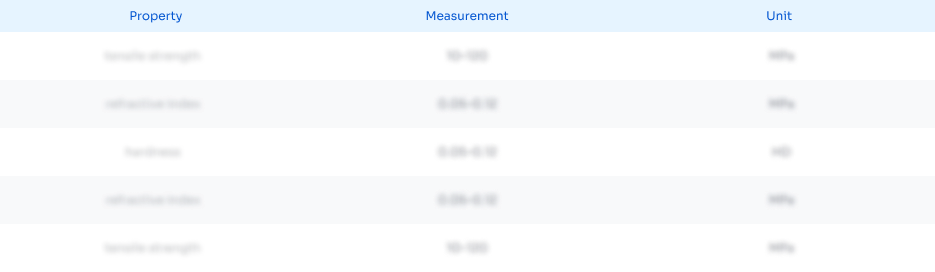
Abstract
Description
Claims
Application Information

- R&D
- Intellectual Property
- Life Sciences
- Materials
- Tech Scout
- Unparalleled Data Quality
- Higher Quality Content
- 60% Fewer Hallucinations
Browse by: Latest US Patents, China's latest patents, Technical Efficacy Thesaurus, Application Domain, Technology Topic, Popular Technical Reports.
© 2025 PatSnap. All rights reserved.Legal|Privacy policy|Modern Slavery Act Transparency Statement|Sitemap|About US| Contact US: help@patsnap.com