A method for measuring the angle of boresight of a spatially distributed camera
A camera boresight and test method technology, applied in the field of aerospace optical remote sensors, can solve problems such as difficulty and large scale, and achieve the effects of improving test accuracy, shortening test cycle, and saving test costs
- Summary
- Abstract
- Description
- Claims
- Application Information
AI Technical Summary
Problems solved by technology
Method used
Image
Examples
Embodiment Construction
[0022] The basic idea of the present invention is to use a three-sided reflecting prism and a high-precision precision goniometer to realize the angle test of the visual axis of a spatially distributed camera. The installation location of the test equipment such as Figure 4 As shown, the specific implementation is as follows:
[0023] Step (1) Determine the angle between the two adjacent reflective surfaces of the three-sided reflective prism 3 so that the angle between the adjacent reflective surfaces of the three-sided reflective prism 3 is 180°-Φ; where Φ is the phase of the three-line array camera 2 under test Design value of the angle of sight of adjacent camera;
[0024] Step (2) Use the precision goniometer 1 to test the actual values of the two included angles θ and β of the adjacent reflective surfaces of the three-sided reflective prism 3, such as image 3 As shown, θ and β are the actual test values of the included angle between adjacent reflecting surfaces, and ...
PUM
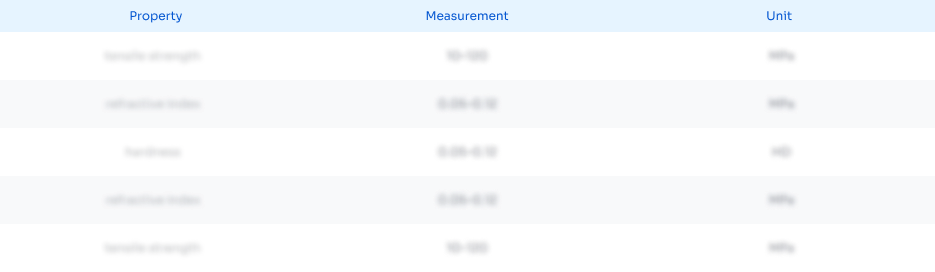
Abstract
Description
Claims
Application Information

- Generate Ideas
- Intellectual Property
- Life Sciences
- Materials
- Tech Scout
- Unparalleled Data Quality
- Higher Quality Content
- 60% Fewer Hallucinations
Browse by: Latest US Patents, China's latest patents, Technical Efficacy Thesaurus, Application Domain, Technology Topic, Popular Technical Reports.
© 2025 PatSnap. All rights reserved.Legal|Privacy policy|Modern Slavery Act Transparency Statement|Sitemap|About US| Contact US: help@patsnap.com