Hydrocarbon catalytic conversion method of productive butene
A catalytic conversion method and technology for hydrocarbons, which are applied in the fields of hydrocarbon cracking to produce hydrocarbons, treatment of hydrocarbon oil, organic chemistry, etc., can solve the problems of low butene yield, etc., and achieve the effects of high butene yield and high process flexibility.
- Summary
- Abstract
- Description
- Claims
- Application Information
AI Technical Summary
Problems solved by technology
Method used
Image
Examples
Embodiment 1
[0086] The cracking catalyst used in this embodiment is: based on the total weight of the cracking catalyst, the cracking catalyst used contains 10% by weight of beta zeolite, 20% by weight of ZSM-5 zeolite (the ratio of silicon to aluminum is 40), 45% by weight of Kaolin and 25% by weight of alumina binder, wherein the beta zeolite contains 1% by weight of iron and 1.5% by weight of phosphorus in terms of elements. The cracking catalyst is aged for 10 hours at 800°C and 100% water vapor atmosphere, and the catalyst loading in the device (system catalyst storage) is 60 kg.
[0087] The first hydrocarbon raw material (its properties are shown in Table 1) is introduced into the riser reactor 1, and after being contacted with the hot catalyst from the regenerator 7, the reaction oil gas is separated from the catalyst, and the separated coke catalyst is introduced into the stripper 6. After being stripped, it is transported to the regenerator 7 for regeneration, and the reaction o...
Embodiment 2
[0089] The process and the cracking catalyst used in this example are the same as those in Example 1, except that the weight ratio of the unborn cracking catalyst introduced into the fluidized bed reactor 2 to the regenerated cracking catalyst is 90:10.
Embodiment 3
[0102] The flow process of this embodiment is the same as that of Example 1. The difference is that the cracking catalyst used is: based on the total weight of the cracking catalyst, the cracking catalyst used contains 15% by weight of zeolite beta, 15% by weight of ZSM-5 zeolite (silicon Aluminum ratio is 40), 45% by weight of kaolin and 25% by weight of alumina binder, wherein, zeolite beta contains 1% by weight of iron and 1.5% by weight of phosphorus in terms of elements; and, reaction conditions and reaction results See Table 4.
PUM
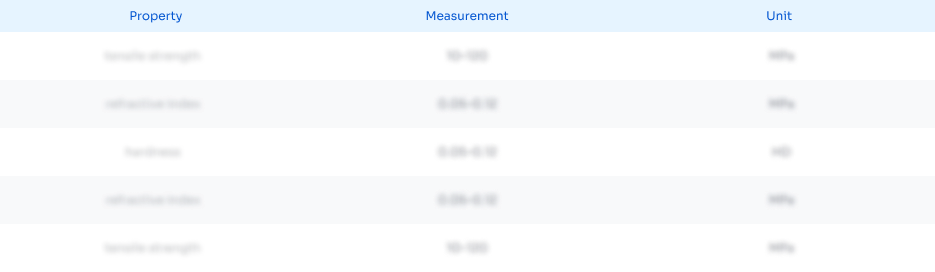
Abstract
Description
Claims
Application Information

- R&D
- Intellectual Property
- Life Sciences
- Materials
- Tech Scout
- Unparalleled Data Quality
- Higher Quality Content
- 60% Fewer Hallucinations
Browse by: Latest US Patents, China's latest patents, Technical Efficacy Thesaurus, Application Domain, Technology Topic, Popular Technical Reports.
© 2025 PatSnap. All rights reserved.Legal|Privacy policy|Modern Slavery Act Transparency Statement|Sitemap|About US| Contact US: help@patsnap.com