Process for producing automobile tyre
A production process and technology for automobile tires, applied in tires, other household appliances, household appliances, etc., which can solve the problems of physical and mechanical properties and process technical operation performance, uneven thickness of rubber on both sides of cords, and parts size and weight. Too much conformity and other problems to achieve the effect of ensuring effectiveness and safety, improving size and weight, and improving uniformity
- Summary
- Abstract
- Description
- Claims
- Application Information
AI Technical Summary
Problems solved by technology
Method used
Examples
Embodiment 1
[0023] The process is divided into five steps, firstly carry out (1) batching internal mixing: it is divided into three steps of material selection, acidification and temperature adjustment, in which the raw materials selected in the material selection process include carbon black and natural rubber, and 10% of the acidification process is added Dilute sulfuric acid, adjust the temperature to 320 degrees Celsius in the temperature adjustment process; then proceed to (2) rubber parts preparation: divided into extrusion, calendering, bead forming and cord cutting, and the equipment used in the extrusion process is four composite extruders , The process of pressing the rubber core is divided into positioning, heating, pressure regulation and extrusion. In the heating process, the temperature is raised to 300 degrees Celsius, and in the calendering process, the temperature is adjusted to 380 degrees Celsius, and then (3) Semi-finished product processing: divided into pressing tread:...
Embodiment 2
[0025] Repeat Example 1 according to the same steps described, the difference is: in the acidification process in step (1), add 15% dilute sulfuric acid, adjust the temperature to 335 degrees Celsius in the temperature adjustment process; step (2) heat up in the heating process Adjust the temperature to 310 degrees Celsius, adjust the temperature to 380 degrees Celsius in the calendering process, adjust the temperature to 405 degrees Celsius in the step (3) medium-pressure tread process, adjust the temperature to 395 degrees Celsius in the bead side process, and adjust the temperature to 435 degrees Celsius in the rubber pad process The temperature is adjusted to 385 degrees Celsius for the rubber core process. In step (4), hot 15% sodium hydroxide solution is added to the semi-finished product process. During the assembly process, the temperature is adjusted to 280 degrees Celsius and kept for 50 minutes. Step (5) Adjust the temperature to 235 degrees Celsius.
Embodiment 3
[0027] Repeat Example 1 according to the same steps as described, the difference is: add 10% dilute sulfuric acid in the acidification process in step (1), and adjust the temperature to 320 degrees Celsius in the temperature adjustment process; step (2) heat up in the heating process Adjust the temperature to 300 degrees Celsius, adjust the temperature to 380 degrees Celsius in the calendering process, adjust the temperature to 410 degrees Celsius in the step (3) medium pressure tread process, adjust the temperature to 400 degrees Celsius in the bead side process, and adjust the temperature to 440 degrees Celsius in the pressure pad process The temperature is adjusted to 390 degrees Celsius for the rubber core process. In step (4), hot 20% sodium hydroxide solution is added to the semi-finished product process. During the assembly process, the temperature is adjusted to 290 degrees Celsius and kept for 60 minutes. Step (5) Adjust the temperature to 250°C.
[0028] Te...
PUM
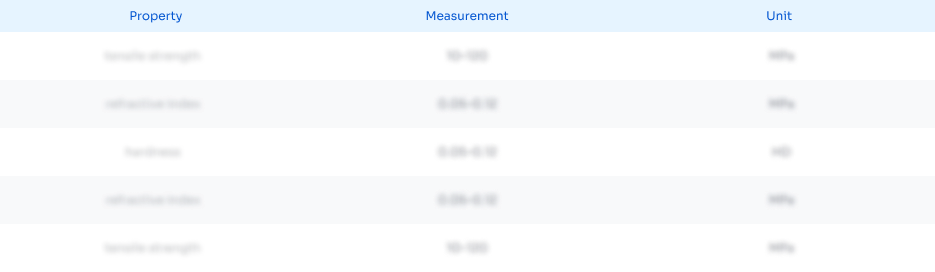
Abstract
Description
Claims
Application Information

- R&D
- Intellectual Property
- Life Sciences
- Materials
- Tech Scout
- Unparalleled Data Quality
- Higher Quality Content
- 60% Fewer Hallucinations
Browse by: Latest US Patents, China's latest patents, Technical Efficacy Thesaurus, Application Domain, Technology Topic, Popular Technical Reports.
© 2025 PatSnap. All rights reserved.Legal|Privacy policy|Modern Slavery Act Transparency Statement|Sitemap|About US| Contact US: help@patsnap.com