A kind of preparation method of hydrophilic anti-fouling polyvinylidene fluoride film
A polyvinylidene fluoride membrane and anti-pollution technology, applied in chemical instruments and methods, membrane technology, semi-permeable membrane separation, etc., can solve the problems of human hazards, vulnerable structures, restrictions, etc., and achieve low equipment requirements, Good anti-pollution performance, easy to operate effect
- Summary
- Abstract
- Description
- Claims
- Application Information
AI Technical Summary
Problems solved by technology
Method used
Image
Examples
Embodiment 1
[0025] 1) Preparation of PVDF original membrane:
[0026] Take 4g of PVDF powder and 1g of polyvinylpyrrolidone dissolved in 34mL N,N-dimethylacetamide (DMAc) to prepare a 15wt% PVDF casting solution, stir evenly at 70°C, vacuum defoam, and then use a 300µm spatula to remove the casting solution Spread it on a glass plate and place it in a coagulation bath at 65°C (DMAc / distilled water = 30 / 70, w / w); wait until the PVDF membrane is separated from the glass plate, then take it out and soak it in secondary water for 48 hours , dried to obtain the original PVDF film;
[0027] 2) Chemical modification of PVDF membrane surface:
[0028] Put 4 pieces of original PVDF membranes (4cm×4cm) into a flask filled with 35mL of a mixed solution of methanol and water (45 / 55, w / w), and add 0.1g of sulfobetaine methacrylate (SBMA ) and 0.005g of pentamethyldiethylenetriamine; nitrogen gas was passed for 30 minutes to remove the air, then 0.001g of cuprous chloride was added therein, and heate...
Embodiment 2
[0031] 1) Preparation of PVDF original membrane:
[0032] Dissolve 6g of PVDF powder and 1g of polyvinylpyrrolidone in 34mL of N,N-dimethylacetamide (DMAc) to prepare a 20wt% PVDF casting solution, stir evenly at 75°C, vacuum defoam, and then spray the casting solution with a 300µm Spread the spatula on the glass plate and place it in a coagulation bath at 65°C (DMAc / distilled water = 30 / 70, w / w); wait until the PVDF membrane is separated from the glass plate, take it out and soak it in secondary water for 48 Hours, dry to get PVDF original film.
[0033] 2) Chemical modification of PVDF membrane surface:
[0034] Put 4 pieces of PVDF original membranes (4 cm × 4 cm) into a flask filled with 35 mL of a mixed solution of methanol and water (45 / 55, w / w), and add 0.1 g sulfobetaine methacrylate ( SBMA) and 0.005g pentamethyldiethylenetriamine; Nitrogen was passed for 30 minutes to remove the air, then 0.005 g of cuprous chloride was added to it, heated to 40°C for 6 hours; the ...
Embodiment 3
[0037] 1) Preparation of PVDF original membrane:
[0038] Dissolve 4g of PVDF powder and 0.5g of polyvinylpyrrolidone in 34mL of N,N-dimethylacetamide (DMAc) to prepare a 15wt% PVDF casting solution, stir evenly at 75°C, vacuum defoam, and then use the casting solution with Spread a 300µm spatula on a glass plate and place it in a coagulation bath at 65°C (DMAc / distilled water = 30 / 70, w / w); wait until the PVDF membrane is separated from the glass plate, then take it out and soak it in secondary water After 48 hours, dry to obtain the original PVDF film.
[0039] 2) Chemical modification of PVDF membrane surface:
[0040] Put 4 pieces of PVDF original membranes (4cm×4cm) into a flask filled with 35mL of a mixed solution of methanol and water (45 / 55, w / w), and add 0.2g of sulfobetaine methacrylate (SBMA) and 0.01 g of pentamethyldiethylenetriamine. Nitrogen was blown for 30 minutes to remove the air, then 0.002 g of cuprous chloride was added thereto, and heated to 40° C. fo...
PUM
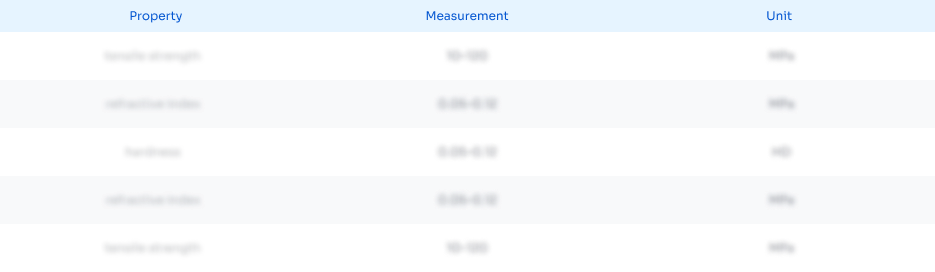
Abstract
Description
Claims
Application Information

- R&D
- Intellectual Property
- Life Sciences
- Materials
- Tech Scout
- Unparalleled Data Quality
- Higher Quality Content
- 60% Fewer Hallucinations
Browse by: Latest US Patents, China's latest patents, Technical Efficacy Thesaurus, Application Domain, Technology Topic, Popular Technical Reports.
© 2025 PatSnap. All rights reserved.Legal|Privacy policy|Modern Slavery Act Transparency Statement|Sitemap|About US| Contact US: help@patsnap.com