Back-stepping direct power control method of DFIG
A power control and direct technology, applied in control systems, control generators, vector control systems, etc., can solve the problems of complex vector selection, high dependence on mathematical model parameters, and weak robustness.
- Summary
- Abstract
- Description
- Claims
- Application Information
AI Technical Summary
Problems solved by technology
Method used
Image
Examples
Embodiment Construction
[0029] In order to describe the present invention more specifically, the technical solutions of the present invention will be described in detail below with reference to the accompanying drawings and specific embodiments.
[0030] The DFIG inverse direct power control system of this embodiment includes a 2MW DFIG1, a voltage source converter 2 connected to the DFIG rotor winding, a voltage sensor 3 for detecting the three-phase voltage of the DFIG stator, and a voltage sensor 3 for detecting the three-phase voltage of the DFIG stator. The current Hall sensor 4 of the phase current, the encoder 11 for detecting the rotor position angle of the DFIG, the differentiator 10 for obtaining the rotational speed of the unit, and the control loop for realizing the regulation of the active and reactive power of the DFIG output. The control loop is composed of a feedback signal processing channel and a forward control channel, wherein the forward control channel includes a SVPWM signal gen...
PUM
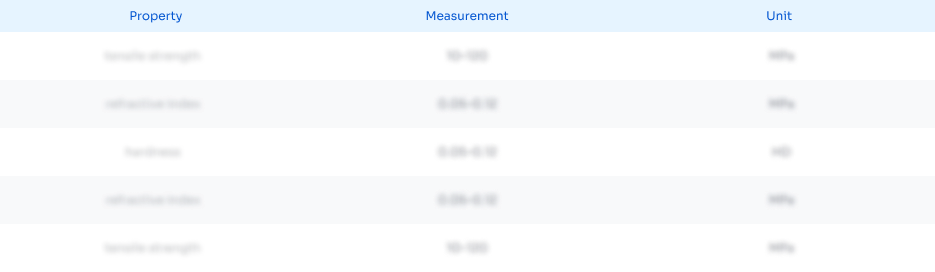
Abstract
Description
Claims
Application Information

- Generate Ideas
- Intellectual Property
- Life Sciences
- Materials
- Tech Scout
- Unparalleled Data Quality
- Higher Quality Content
- 60% Fewer Hallucinations
Browse by: Latest US Patents, China's latest patents, Technical Efficacy Thesaurus, Application Domain, Technology Topic, Popular Technical Reports.
© 2025 PatSnap. All rights reserved.Legal|Privacy policy|Modern Slavery Act Transparency Statement|Sitemap|About US| Contact US: help@patsnap.com