Heat storage burning system
A heat supply system and heat storage technology, applied in the direction of incinerators, combustion methods, combustion types, etc., can solve problems such as prone to danger, inability to lengthen air ducts, and slow feedback speed of concentration detectors, so as to reduce pollution and ensure equipment safety Reliable, easy-to-maintain results
- Summary
- Abstract
- Description
- Claims
- Application Information
AI Technical Summary
Problems solved by technology
Method used
Image
Examples
Embodiment 1
[0028] The thermal storage incineration system provided by this embodiment has a structure such as figure 1 with 2 Shown, including heating system, combustion-supporting solvent system, thermal storage oxidation system, air intake system, exhaust system and flue gas spray system, air intake system, combustion-supporting solvent system and air intake system are connected in series with the thermal storage oxidation system. The inlet is connected in parallel with the intake system, combustion-supporting solvent system and the intake system. The outlet of the thermal storage oxidation system is connected in series with the exhaust system, and the exhaust system is connected to the flue gas spray system. Among them:
[0029] The heat storage oxidation system includes a heat storage chamber 2 and an oxidation chamber 1. The oxidation chamber 1 is also equipped with a permanent flame burner 23 and a flame detector. The top of the oxidation chamber 1 is equipped with an explosion-proof op...
PUM
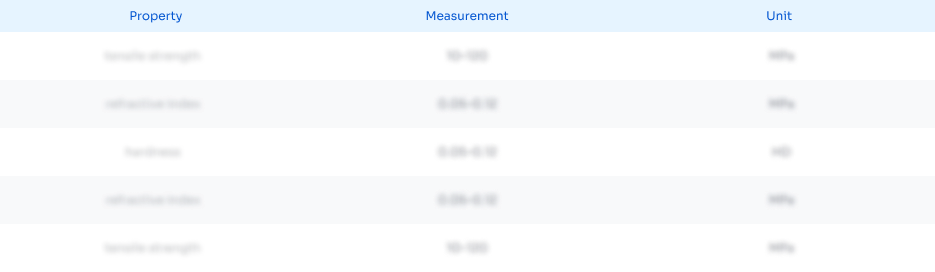
Abstract
Description
Claims
Application Information

- Generate Ideas
- Intellectual Property
- Life Sciences
- Materials
- Tech Scout
- Unparalleled Data Quality
- Higher Quality Content
- 60% Fewer Hallucinations
Browse by: Latest US Patents, China's latest patents, Technical Efficacy Thesaurus, Application Domain, Technology Topic, Popular Technical Reports.
© 2025 PatSnap. All rights reserved.Legal|Privacy policy|Modern Slavery Act Transparency Statement|Sitemap|About US| Contact US: help@patsnap.com