Multistage stretching heat shaping method of polyphenylene sulfide filament
A technology of polyphenylene sulfide and heat setting, which is applied in the direction of textiles and papermaking, can solve the problems of being unsuitable for industrial production, staying in the experimental stage, and less filament production, so as to improve production stability, stabilize the aggregate structure, The effect of stable production process
- Summary
- Abstract
- Description
- Claims
- Application Information
AI Technical Summary
Problems solved by technology
Method used
Image
Examples
Embodiment Construction
[0029] figure 1 Shown is the polyphenylene sulfide filament multi-stage stretching heat setting device used in the present invention, which includes the following components arranged in sequence: wire bobbin frame 1, first wire guide rod 3, second guide wire Rod 5, roller front rotor 6, roller, I disk 10, II disk 11, III disk 12, high temperature hot plate 13, IV disk 14, traverse device 15, friction roller 16 and wire drum 17. Wherein, the rubber apron 7 and the guide roller 8 of pressing contact are arranged on the roller. The polyphenylene sulfide primary fiber (PPS-UDY) reel 2 is placed on the wire reel frame 1, and the rotation of the rollers and all the hot plates is driven by the frequency conversion motor 9. The wheelbase between rollers and Ι is 350mm, the wheelbase between Ι and Ⅱ is 450mm, the wheelbase between Ⅱ and Ⅲ is 550mm, and the wheelbase between Ⅲ and Ⅳ is 750mm. The fineness of a single fiber is 15-17dtex.
[0030] A multi-stage drawing heat-setting met...
PUM
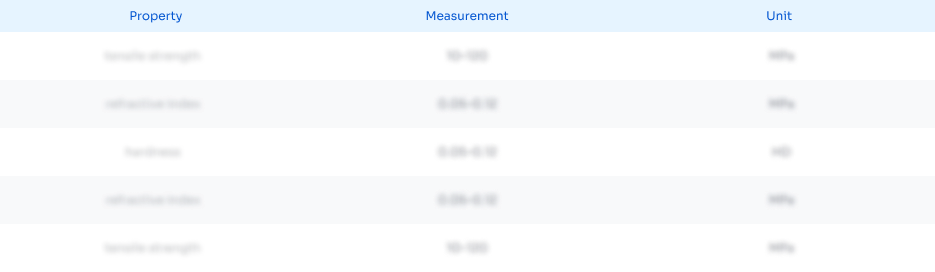
Abstract
Description
Claims
Application Information

- Generate Ideas
- Intellectual Property
- Life Sciences
- Materials
- Tech Scout
- Unparalleled Data Quality
- Higher Quality Content
- 60% Fewer Hallucinations
Browse by: Latest US Patents, China's latest patents, Technical Efficacy Thesaurus, Application Domain, Technology Topic, Popular Technical Reports.
© 2025 PatSnap. All rights reserved.Legal|Privacy policy|Modern Slavery Act Transparency Statement|Sitemap|About US| Contact US: help@patsnap.com