Carbon oil pcb board and manufacturing method thereof
A technology of PCB board and manufacturing method, which is applied in the direction of printed circuit manufacturing, printed circuit parts, electrical components, etc., can solve the problems of uneven thickness, difficult to control the thickness of carbon film, and difficult to control the resistance of carbon film, and achieve thickness Uniform, good carbon film resistance, high yield
- Summary
- Abstract
- Description
- Claims
- Application Information
AI Technical Summary
Problems solved by technology
Method used
Image
Examples
Embodiment Construction
[0018] In order to make the object, technical solution and advantages of the present invention clearer, the present invention will be further described in detail below in conjunction with the accompanying drawings and embodiments. It should be understood that the specific embodiments described here are only used to explain the present invention, not to limit the present invention.
[0019] see figure 1 , a kind of carbon oil PCB board manufacturing method provided by the embodiment of the present invention, comprises the following steps:
[0020] Prepare carbon ink S1: fully stir the carbon ink to make it reach the required viscosity, and the required viscosity ranges from 350 to 400dpa.s;
[0021] Cutting S2: solidify the solder resist on the PCB substrate, then make carbon ink graphics to be printed on the PCB board with solder resist cured, and then install it on the screen printing machine;
[0022] Plate-making S3: Make the screen, make the screen tension 20-30N / cm, ins...
PUM
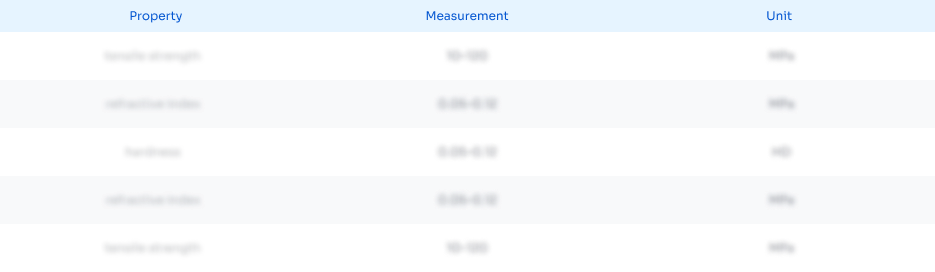
Abstract
Description
Claims
Application Information

- R&D
- Intellectual Property
- Life Sciences
- Materials
- Tech Scout
- Unparalleled Data Quality
- Higher Quality Content
- 60% Fewer Hallucinations
Browse by: Latest US Patents, China's latest patents, Technical Efficacy Thesaurus, Application Domain, Technology Topic, Popular Technical Reports.
© 2025 PatSnap. All rights reserved.Legal|Privacy policy|Modern Slavery Act Transparency Statement|Sitemap|About US| Contact US: help@patsnap.com