Stainless steel golf club head manufacturing method
A technology for golf club heads and manufacturing methods, applied to golf balls, golf clubs, sports accessories, etc., which can solve the problems of loss of smelted casting metal, difficult reduction of casting cost, and increase of casting cost, so as to improve the convenience of operation performance, reduce weight loss rate, improve yield and quality
- Summary
- Abstract
- Description
- Claims
- Application Information
AI Technical Summary
Problems solved by technology
Method used
Image
Examples
Embodiment Construction
[0063] In order to make the above-mentioned and other objects, features and advantages of the present invention more comprehensible, the preferred embodiments of the present invention are specifically cited below, together with the accompanying drawings, and are described in detail as follows:
[0064] see figure 1 , which is a vacuum centrifugal casting device used in conjunction with the manufacturing method of the stainless steel golf club head of the present invention. Wherein, the vacuum centrifugal casting device comprises a vacuum furnace 1, a rotating shaft 2, a rotating platform 3, a shell mold 4 and a heater 5; the rotating shaft 2, rotating platform 3, shell mold 4 and heater 5 are all located on In the vacuum furnace 1 , the rotating platform 3 is connected to the rotating shaft 2 to rotate synchronously with the rotating shaft 2 , the shell mold 4 is positioned on the rotating platform 3 , and the heater 5 is used to heat the shell mold 4 .
[0065] More specific...
PUM
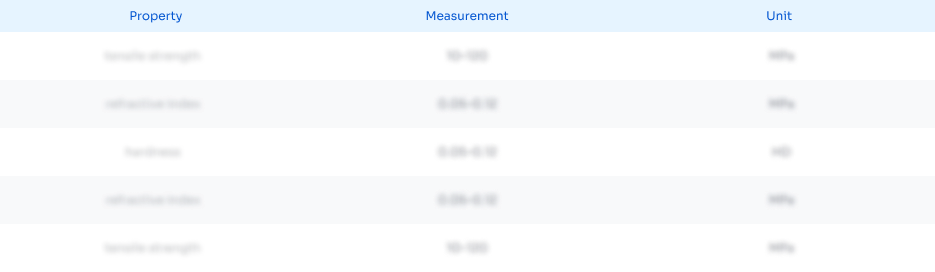
Abstract
Description
Claims
Application Information

- R&D Engineer
- R&D Manager
- IP Professional
- Industry Leading Data Capabilities
- Powerful AI technology
- Patent DNA Extraction
Browse by: Latest US Patents, China's latest patents, Technical Efficacy Thesaurus, Application Domain, Technology Topic, Popular Technical Reports.
© 2024 PatSnap. All rights reserved.Legal|Privacy policy|Modern Slavery Act Transparency Statement|Sitemap|About US| Contact US: help@patsnap.com