Production system of porcelain tile
A production system and a technology for porcelain tiles, applied in the field of building materials, can solve the problems of not meeting the index requirements, less cinder usage, less usage, etc., and achieve the effects of environmental protection and energy saving, no solid discharge, and resource saving.
- Summary
- Abstract
- Description
- Claims
- Application Information
AI Technical Summary
Problems solved by technology
Method used
Image
Examples
Embodiment Construction
[0056] In order to make the purpose, technical solution and advantages of the present invention clearer, the present invention will be further described in detail below in conjunction with the accompanying drawings.
[0057] Such as figure 1 As shown, the invention provides a production system of porcelain tiles, comprising:
[0058] A cinder pretreatment device 1 for pretreating cinders; connected with the cinder pretreatment device 1, a batching device 2 for mixing and batching raw materials for the production of porcelain tiles. Coal slag processed by the processing device; connected with the batching device 2, a molding device 3 used for pressing and molding the raw materials after mixing and batching; connected with the molding device 3, used for sintering the pressed bricks. Sintering device 4.
[0059] Wherein, the coal slag pretreatment device 1 is used to pretreat the coal slag so that the TiO of the coal slag 2 Content2 o 5 Content<0.05%, Fe content<0.5%. The ci...
PUM
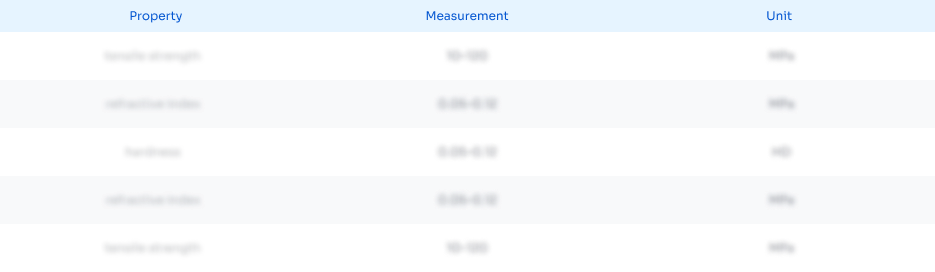
Abstract
Description
Claims
Application Information

- Generate Ideas
- Intellectual Property
- Life Sciences
- Materials
- Tech Scout
- Unparalleled Data Quality
- Higher Quality Content
- 60% Fewer Hallucinations
Browse by: Latest US Patents, China's latest patents, Technical Efficacy Thesaurus, Application Domain, Technology Topic, Popular Technical Reports.
© 2025 PatSnap. All rights reserved.Legal|Privacy policy|Modern Slavery Act Transparency Statement|Sitemap|About US| Contact US: help@patsnap.com