A ceramic wire/cable core manufacturing system
A technology for manufacturing systems and cable cores, applied in cable/conductor manufacturing, circuits, electrical components, etc., can solve problems such as difficult to achieve high-speed production of ceramic wires and cables, and achieve market competitiveness, continuous production, and simple process equipment Effect
- Summary
- Abstract
- Description
- Claims
- Application Information
AI Technical Summary
Problems solved by technology
Method used
Image
Examples
Embodiment 1
[0041] see figure 1, which discloses the longitudinal wrapping mechanism (embodiment 1) of the ceramic wire / cable core manufacturing system of the present invention, including a series-connected storage and release unit 10, a longitudinal wrapping unit 30, and a set of sheath layer extruding unit 40 , cooling and heating unit 50, high-voltage spark machine 60, system equipment of take-up unit 70 and parallel storage and feeding belt unit 20.
[0042] The wire storage and release unit 10 includes an active wire release mechanism 12, a wire / cable core 11, a pair of movable rollers B 14 and three fixed rollers A 13. The arrangement enables the movable roller B 14 to move freely up and down.
[0043] The longitudinal swivel unit 30 includes four fixed roller sets E 31 , the horn bundle mold 32 and the wire / cable core 11, in order of the direction of travel of the wire / cable core 11, the fixed roller set E 31 is connected in series to the horn The upstream of the bundle mold 32 a...
Embodiment 2
[0049] see figure 2 , which discloses the winding and covering mechanism (embodiment 2) of the ceramic wire / cable core manufacturing system of the present invention, including the storage and release line unit 10 in series, two winding units 100 clockwise and counterclockwise, a set of protective Jacket extruding unit 40, cooling and heating unit 50, high-voltage spark machine 60, take-up unit 70" system equipment.
[0050] The pay-off unit 10 includes an active pay-off machine 12, a wire / cable core 11 and a tension control system 71. The tension control system 71 is arranged at the take-up end. The pay-off mechanism 12 and the tension control system 71 use PLC to control the line speed and tension.
[0051] The winding unit 100 includes a belt feeding mechanism 110, a revolving hollow shaft 120, a bracket 130 and a revolving motor 140; in order of the direction of travel of the wire / cable core 11, two sets of winding units 100 are immediately adjacent to and connected in ser...
PUM
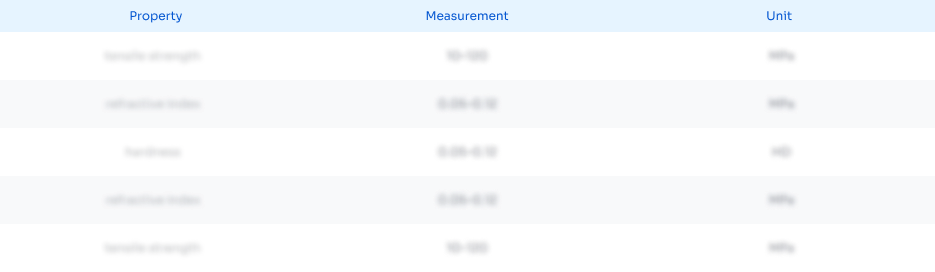
Abstract
Description
Claims
Application Information

- R&D
- Intellectual Property
- Life Sciences
- Materials
- Tech Scout
- Unparalleled Data Quality
- Higher Quality Content
- 60% Fewer Hallucinations
Browse by: Latest US Patents, China's latest patents, Technical Efficacy Thesaurus, Application Domain, Technology Topic, Popular Technical Reports.
© 2025 PatSnap. All rights reserved.Legal|Privacy policy|Modern Slavery Act Transparency Statement|Sitemap|About US| Contact US: help@patsnap.com