Polyurethane composite material regenerated from waste polyurethane soles and preparation process thereof
A composite material and polyurethane technology, applied in the chemical industry, can solve the problems of land occupation, environmental pollution, waste of resources, etc., and achieve the effects of environmental protection, no discharge of three wastes, and solution to recycling problems
- Summary
- Abstract
- Description
- Claims
- Application Information
AI Technical Summary
Problems solved by technology
Method used
Examples
Embodiment 1
[0017] A recycled polyurethane composite material using waste polyurethane soles, prepared from the following raw materials in parts by weight (kg): waste polyurethane soles 170, compatibilizer 10, toluene diisocyanate 5, tris(2,4-di-tert-butylphenol ) phosphite 2, medical stone powder 4, silicone 6, ammonium polyphosphate 2, polyisocyanate 12, mixed polyester polyol 3, dibutyltin dilaurate 5, alkyl alcohol amide 6, nano-alumina powder 4, Antioxidant TNP 2, aluminum stearate 7, isocyanate 8, zirconia 4, nano-montmorillonite 9, auxiliary agent 10; the auxiliary agent is made of the following raw materials in parts by weight (kg): aluminum tripolyphosphate 1 , palm wax 2, talcum powder 4, liquid paraffin 2, calcium carbonate 13, ethylene bis stearamide 3, ethyleneimine 1, hydrogenated castor oil 7, sodium stearate 10, graphene 6, epoxy resin 7; The preparation method is: weigh the aluminum tripolyphosphate, palm wax, talcum powder, liquid paraffin and calcium carbonate in the ab...
Embodiment 2
[0023] A recycled polyurethane composite material using waste polyurethane soles, prepared from the following raw materials in parts by weight (kg): waste polyurethane soles 175, compatibilizer 12, toluene diisocyanate 6, tris(2,4-di-tert-butylphenol ) phosphite 3, medical stone powder 5, silicone 7, ammonium polyphosphate 2.5, polyisocyanate 15, mixed polyester polyol 4, dibutyltin dilaurate 6, alkanolamide 7, nano-alumina powder 4.5, Antioxidant TNP 2.5, aluminum stearate 8, isocyanate 9, zirconia 5, nano-montmorillonite 10, auxiliary agent 11; the auxiliary agent is made of the following raw materials in parts by weight (kg): aluminum tripolyphosphate 1.5 , palm wax 2.5, talcum powder 4.5, liquid paraffin 2.5, calcium carbonate 14.5, ethylene bis stearamide 3.5, ethyleneimine 1.5, hydrogenated castor oil 8, sodium stearate 11, graphene 7, epoxy resin 10; The preparation method is: weigh the aluminum tripolyphosphate, palm wax, talcum powder, liquid paraffin and calcium carb...
Embodiment 3
[0026] A recycled polyurethane composite material using waste polyurethane soles, prepared from the following raw materials in parts by weight (kg): waste polyurethane soles 180, compatibilizer 14, toluene diisocyanate 7, tris(2,4-di-tert-butylphenol ) phosphite 4, medical stone powder 6, silicone 8, ammonium polyphosphate 3, polyisocyanate 18, mixed polyester polyol 5, dibutyltin dilaurate 7, alkyl alcohol amide 8, nano-alumina powder 5, Antioxidant TNP 3, aluminum stearate 9, isocyanate 10, zirconia 6, nano-montmorillonite 11, auxiliary agent 12; the auxiliary agent is made of the following raw materials in parts by weight (kg): aluminum tripolyphosphate 2 , palm wax 3, talcum powder 5, liquid paraffin 3, calcium carbonate 16, ethylene bis stearamide 4, ethyleneimine 2, hydrogenated castor oil 9, sodium stearate 12, graphene 8, epoxy resin 13; The preparation method is: weigh the aluminum tripolyphosphate, palm wax, talcum powder, liquid paraffin and calcium carbonate in the...
PUM
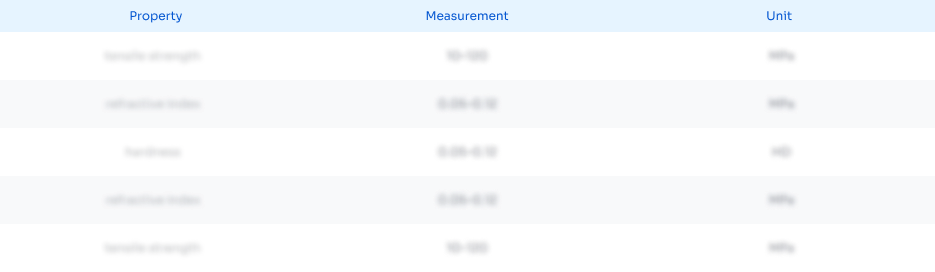
Abstract
Description
Claims
Application Information

- R&D
- Intellectual Property
- Life Sciences
- Materials
- Tech Scout
- Unparalleled Data Quality
- Higher Quality Content
- 60% Fewer Hallucinations
Browse by: Latest US Patents, China's latest patents, Technical Efficacy Thesaurus, Application Domain, Technology Topic, Popular Technical Reports.
© 2025 PatSnap. All rights reserved.Legal|Privacy policy|Modern Slavery Act Transparency Statement|Sitemap|About US| Contact US: help@patsnap.com