Multi-step continuous resin transfer molding method for rail vehicle composite components
A composite material component and resin transfer molding technology, which is used in the design and manufacture of resin-based fiber reinforced composite products to achieve the effects of shortening the resin flow length, shortening the curing time, and preventing air bubbles or dry spots.
- Summary
- Abstract
- Description
- Claims
- Application Information
AI Technical Summary
Problems solved by technology
Method used
Image
Examples
Embodiment Construction
[0024] Such as figure 1 As shown, a multi-step continuous RTM molding method consists of an upper mold 1, a lower mold 2, a clamping and locking mechanism 3, two sets of movable electric heating tube arrays 4, several resin filling pipe joints 5, several pumping It consists of a vacuum joint 6 and a molding parameter control system 7. Wherein, the upper mold 1, the lower mold 2, and the clamping and locking mechanism 3 jointly constitute the molding mold for multi-step continuous RTM molding; the two groups of movable electric heating tube arrays 4 are installed on the platform of the mobile trolley 8, Placed under the lower mold 2 during work, it is used to heat the lower mold 2 to solidify the resin injected into the cavity of the mold. The moving speed and platform height of the mobile trolley 8 are set by the molding parameter control system 7; The control of the heating range of the designated area of the lower die 2 is achieved by adjusting the height of the platform ...
PUM
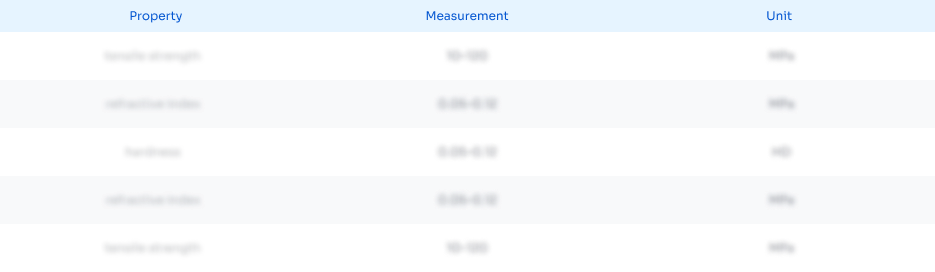
Abstract
Description
Claims
Application Information

- Generate Ideas
- Intellectual Property
- Life Sciences
- Materials
- Tech Scout
- Unparalleled Data Quality
- Higher Quality Content
- 60% Fewer Hallucinations
Browse by: Latest US Patents, China's latest patents, Technical Efficacy Thesaurus, Application Domain, Technology Topic, Popular Technical Reports.
© 2025 PatSnap. All rights reserved.Legal|Privacy policy|Modern Slavery Act Transparency Statement|Sitemap|About US| Contact US: help@patsnap.com