Edge cutting device for film roll
A film roll and edge trimming technology, applied in metal processing and other directions, can solve the problems of wasting time in product connection, breaking the film and wrapping it on the roll, affecting production efficiency, etc., to avoid difficulty in moving, avoid displacement and error, The effect of improving production efficiency
- Summary
- Abstract
- Description
- Claims
- Application Information
AI Technical Summary
Problems solved by technology
Method used
Image
Examples
Embodiment Construction
[0021] Such as figure 1 As shown, the thin film roll edge trimming device of the present invention includes an electromagnetic base 1 , a frequency conversion motor 2 , a screw lifting device 3 , an edge trimming knife 4 and an edge trimming knife adjusting rod 5 . The spiral lifting device 3 is installed on the electromagnetic base 1, the frequency conversion motor 2 is connected with the spiral lifting device 3, the edge trimming knife adjusting rod 5 is installed on the spiral lifting device 3, and the edge trimming knife 4 is installed on the edge trimming knife adjusting rod 5.
[0022] Such as figure 2 As shown, the screw lifting device 3 includes a bushing 31 , a screw 32 , a worm wheel 33 , a worm 34 , a tapered roller bearing 35 , a thrust bearing (not shown in the figure) and a worm wheel housing 36 . The casing 31 is installed on the electromagnetic base 1 , and the screw rod 32 is installed in the casing 31 . The worm gear housing 36 is installed on the casing 3...
PUM
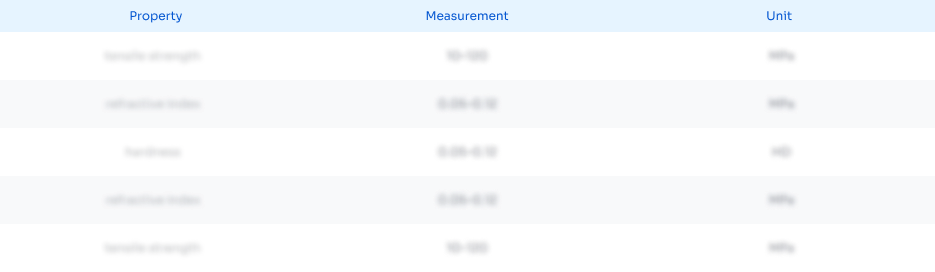
Abstract
Description
Claims
Application Information

- R&D
- Intellectual Property
- Life Sciences
- Materials
- Tech Scout
- Unparalleled Data Quality
- Higher Quality Content
- 60% Fewer Hallucinations
Browse by: Latest US Patents, China's latest patents, Technical Efficacy Thesaurus, Application Domain, Technology Topic, Popular Technical Reports.
© 2025 PatSnap. All rights reserved.Legal|Privacy policy|Modern Slavery Act Transparency Statement|Sitemap|About US| Contact US: help@patsnap.com