Machining method of tension bush clamp for shifting fork groove of automobile gear sleeve
A technology of expanding sleeve fixtures and processing methods, which is applied in the processing field of expanding sleeve fixtures, and can solve problems such as relative movement between gear sleeves and expanding sleeve fixtures.
- Summary
- Abstract
- Description
- Claims
- Application Information
AI Technical Summary
Problems solved by technology
Method used
Image
Examples
Embodiment Construction
[0028] Below in conjunction with accompanying drawing and specific embodiment the present invention will be described in further detail:
[0029] The reference signs in the accompanying drawings of the specification include: front connection plate 1, connection seat 2, positioning seat 3, elastic expansion sleeve 4, expansion part 5, connection part 6, external spline 7, pull rod 8, middle rod 9, positioning concave Groove 10, set screw 11, slider 12, tail rod 13, cavity 14, expansion port 15.
[0030] Such as figure 2 , image 3 As shown, the processing method of the expansion sleeve fixture used for the shift fork groove of the automobile gear sleeve includes the processing steps of the front connecting plate 1, the connecting seat 2 and the positioning seat 3 connected in sequence, and also includes the processing steps of the elastic expansion sleeve 4 and the tie rod 8 ;
[0031] The processing steps of elastic expansion sleeve 4 include:
[0032] A. Blanking, the ma...
PUM
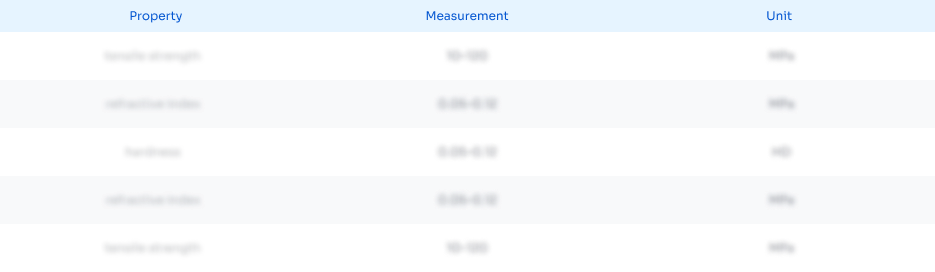
Abstract
Description
Claims
Application Information

- Generate Ideas
- Intellectual Property
- Life Sciences
- Materials
- Tech Scout
- Unparalleled Data Quality
- Higher Quality Content
- 60% Fewer Hallucinations
Browse by: Latest US Patents, China's latest patents, Technical Efficacy Thesaurus, Application Domain, Technology Topic, Popular Technical Reports.
© 2025 PatSnap. All rights reserved.Legal|Privacy policy|Modern Slavery Act Transparency Statement|Sitemap|About US| Contact US: help@patsnap.com