Rear casing assembly manufacturing method capable of solving problems of deformation and cracking
A manufacturing method and component technology, which is applied in the field of rear casing assembly manufacturing, can solve the problems of reducing the stress concentration and stress state of the rear casing assembly, and achieve the effects of avoiding deformation, preventing cracks, and avoiding cracks and deformation
- Summary
- Abstract
- Description
- Claims
- Application Information
AI Technical Summary
Problems solved by technology
Method used
Image
Examples
Embodiment Construction
[0031] The present invention will be further described in detail below in conjunction with the accompanying drawings and specific embodiments.
[0032] The pre-welding parts of the rear casing assembly include 8 webs, 8 support plates, 8 support plate flat tubes, 2 arc strike rings, 1 front mounting edge, 1 rear mounting edge and 1 inner ring, 8 There are 16 longitudinal welds between the web and the heads of the 8 support plates.
[0033] A method for manufacturing a rear casing assembly capable of solving the problems of deformation and cracks includes the following steps:
[0034] Step 1: Use the welding fixture to pre-assemble the web and support plate head. The pre-assembly size is the sum of the design size of the outer casing and the shrinkage deformation size of the weld, and then mark the web according to the pre-assembly size of the outer casing , and then remove the web and mill according to the marking line;
[0035] Step 2: Clean the front and rear mounting edge...
PUM
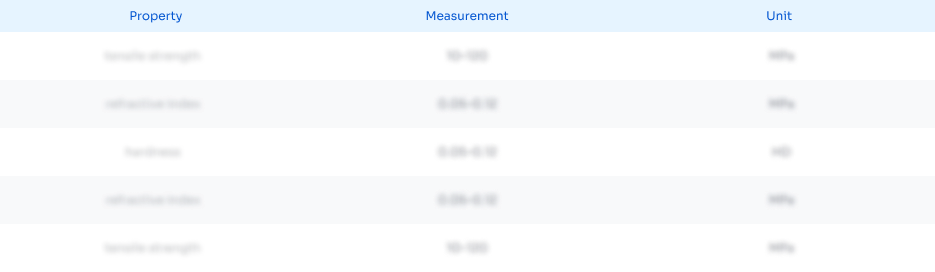
Abstract
Description
Claims
Application Information

- R&D
- Intellectual Property
- Life Sciences
- Materials
- Tech Scout
- Unparalleled Data Quality
- Higher Quality Content
- 60% Fewer Hallucinations
Browse by: Latest US Patents, China's latest patents, Technical Efficacy Thesaurus, Application Domain, Technology Topic, Popular Technical Reports.
© 2025 PatSnap. All rights reserved.Legal|Privacy policy|Modern Slavery Act Transparency Statement|Sitemap|About US| Contact US: help@patsnap.com