Large scale hard alloy butting joint process
A cemented carbide, large-size technology, applied in the field of large-size cemented carbide docking process, can solve the problem that large-size cemented carbide products cannot be fired, and achieve the effect of solving sintering
- Summary
- Abstract
- Description
- Claims
- Application Information
AI Technical Summary
Problems solved by technology
Method used
Image
Examples
Embodiment Construction
[0014] refer to figure 1 , figure 2 It is an embodiment of the large-size cemented carbide butt joint process of the present invention, and the large-size cemented carbide butt joint process includes the following steps in turn:
[0015] A. According to the size of the original to be processed, it is divided into two or three sections and fired into cemented carbide blanks. The firing process is fired according to the existing public carbide firing technology, and the diameter of adjacent blanks differs by 0.5 ~1mm;
[0016] B. Process adjacent blanks to a parallelism of 0.01mm, a flatness of 0.005mm, and a surface roughness of 0.02 microns;
[0017] C. Using the diameter difference of adjacent blanks, apply metal glue on the connection of two adjacent blanks, and then put them back into the furnace for sintering;
[0018] D. During vacuum sintering, the temperature is uniformly raised to 680-720°C and the pressure is 0.5MPa within 2 hours; then the temperature is kept for...
PUM
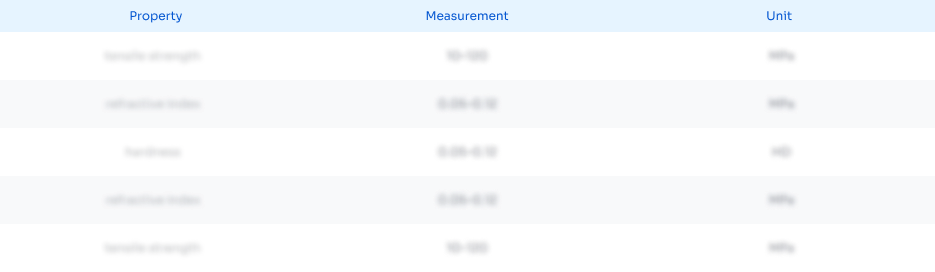
Abstract
Description
Claims
Application Information

- Generate Ideas
- Intellectual Property
- Life Sciences
- Materials
- Tech Scout
- Unparalleled Data Quality
- Higher Quality Content
- 60% Fewer Hallucinations
Browse by: Latest US Patents, China's latest patents, Technical Efficacy Thesaurus, Application Domain, Technology Topic, Popular Technical Reports.
© 2025 PatSnap. All rights reserved.Legal|Privacy policy|Modern Slavery Act Transparency Statement|Sitemap|About US| Contact US: help@patsnap.com