Wet forming production method of dental all-ceramic restoration
A production method, wet forming technology, applied in the direction of dentures, etc., can solve problems such as failure of prosthesis restoration, reduction of long-term stability and reliability of prosthesis, too thin prosthesis cracking, etc., to achieve reduced cracking, high reliability, The effect of a uniform and coherent structure
- Summary
- Abstract
- Description
- Claims
- Application Information
AI Technical Summary
Problems solved by technology
Method used
Image
Examples
Embodiment 1
[0044] For the case and restoration plan: a large area of the posterior tooth is missing, and the posterior zirconia single-crown all-ceramic restoration is made.
[0045] A wet forming manufacturing method for a dental all-ceramic restoration, as attached image 3 shown, including the following steps:
[0046] Step 1: Carry out routine tooth preparation according to the tooth preparation standard of zirconia all-ceramic restoration: the occlusal surface is ground to 1.0 mm to 1.5 mm, the axial surface is ground to 0.8 to 1.0 mm, and the cervical shoulder width is 0.3 to 0.5 mm. The degree of polymerization on the axial surface is 6-8°C, and the corners of each point and line are round and smooth.
[0047] Step 2: Use the 3Shape intraoral scanner TROIS to directly scan the upper and lower dentition to obtain an optical model of the dentition.
[0048] Step 3: Using the dentition optical model obtained in Step 2 as the data source, through the dental restoration design soft...
Embodiment 2
[0055] According to the case and restoration plan: a large area of tooth defect in the posterior teeth, a zirconia-alumina composite single-crown all-ceramic restoration of the posterior teeth was made.
[0056] A wet forming manufacturing method for a dental all-ceramic restoration, as attached image 3 shown, including the following steps:
[0057] Step 1: Carry out routine tooth preparation according to the tooth preparation standard for all-ceramic restorations made of zirconia-alumina composite materials: 1.0 mm to 1.5 mm on the occlusal surface, 0.8 to 1.0 mm on the axial surface, and the width of the cervical shoulder 0.3 ~ 0.5mm, axial surface polymerization degree 6 ~ 8 ℃, and the corners of each point and line are round and smooth.
[0058] Step 2: Take clinical impressions of the upper and lower dentition, use the 3Shape desktop scanner D810 to scan the dentition impression directly, and use the dental restoration design software 3Shape dental CAD system DentalDe...
Embodiment 3
[0066] According to the case and restoration plan: the posterior teeth have large tooth defects, and the posterior teeth are made of aluminum oxide single-crown all-ceramic restorations.
[0067] A wet forming manufacturing method for a dental all-ceramic restoration, as attached Figure 4 shown, including the following steps:
[0068] Step 1: Carry out routine tooth preparation according to the tooth preparation standard of alumina all-ceramic restorations: 1.0mm-1.5mm of the occlusal surface is removed, 0.8-1.0mm of the axial surface is removed, and the cervical shoulder width is 0.3-0.5mm. The degree of polymerization on the axial surface is 6-8°C, and the corners of each point and line are round and smooth.
[0069] Step 2: Use the 3Shape intraoral scanner TROIS to directly scan the upper and lower dentition to obtain an optical model of the dentition.
[0070] Step 3: Using the dentition optical model obtained in Step 2 as the data source, through the dental restoration...
PUM
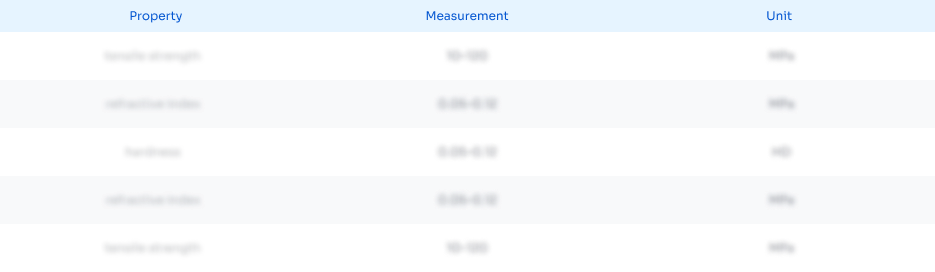
Abstract
Description
Claims
Application Information

- R&D
- Intellectual Property
- Life Sciences
- Materials
- Tech Scout
- Unparalleled Data Quality
- Higher Quality Content
- 60% Fewer Hallucinations
Browse by: Latest US Patents, China's latest patents, Technical Efficacy Thesaurus, Application Domain, Technology Topic, Popular Technical Reports.
© 2025 PatSnap. All rights reserved.Legal|Privacy policy|Modern Slavery Act Transparency Statement|Sitemap|About US| Contact US: help@patsnap.com