Azo pigment composition as well as preparation method thereof and gravure ink composition
A technology of pigment composition and azo pigment, which is applied in the direction of ink, pigment slurry, household appliances, etc., can solve the problems of high gloss, high content of non-ionic surfactant, insufficient tinting strength, etc., and achieve improved gloss , Excellent viscosity stability over time, easy to manufacture
- Summary
- Abstract
- Description
- Claims
- Application Information
AI Technical Summary
Problems solved by technology
Method used
Image
Examples
Embodiment 1
[0095] Using Pigment 1 obtained in Production Example 1, a non-toluene gravure ink was produced. First, 10.0 parts of Pigment 1, 10.0 parts of polyurethane resin, 5.0 parts of resin containing chlorine compounds from DIC Co., Ltd., 11 parts of ethyl acetate, 6 parts of methyl ethyl ketone, 180 parts of steel balls were dispersed for 60 minutes with a paint conditioner (made by Toyo Seiki Co., Ltd.) to obtain a pigment dispersion liquid. Further, 40 parts of polyurethane resin for non-toluene, 11.7 parts of IPA, and 6.3 parts of methyl ethyl ketone were added thereto, and additionally dispersed for 5 minutes with a paint conditioner to obtain a non-toluene polyurethane ink. The viscosity and glossiness of the obtained ink were evaluated.
Embodiment 2
[0097] Except having used the pigment 2 obtained in the manufacture example 2 instead of the pigment 1, the gravure ink was obtained similarly to Example 1, and the viscosity and glossiness were evaluated similarly.
Embodiment 3
[0099] Except having used the pigment 3 obtained in the manufacture example 3 instead of the pigment 1, the gravure ink was obtained similarly to Example 1, and the viscosity and glossiness were evaluated similarly.
PUM
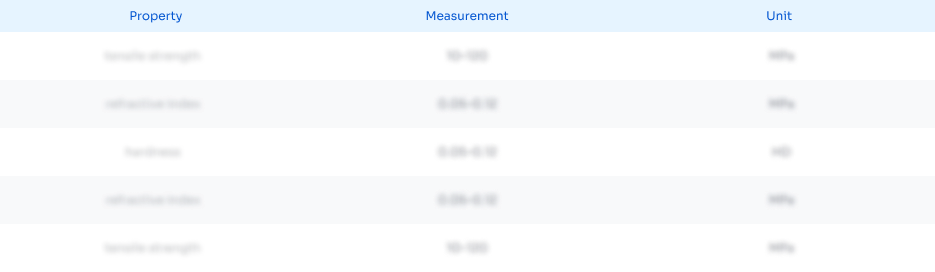
Abstract
Description
Claims
Application Information

- R&D
- Intellectual Property
- Life Sciences
- Materials
- Tech Scout
- Unparalleled Data Quality
- Higher Quality Content
- 60% Fewer Hallucinations
Browse by: Latest US Patents, China's latest patents, Technical Efficacy Thesaurus, Application Domain, Technology Topic, Popular Technical Reports.
© 2025 PatSnap. All rights reserved.Legal|Privacy policy|Modern Slavery Act Transparency Statement|Sitemap|About US| Contact US: help@patsnap.com