Method for treating Claus process tail gas by adopting modified adsorbing agent
A technology of Claus tail gas and process tail gas, which is applied in the field of treating Claus process tail gas with modified adsorbent, can solve the problem of single sulfur component removal, and achieve the effect of reducing energy consumption and device cost
- Summary
- Abstract
- Description
- Claims
- Application Information
AI Technical Summary
Problems solved by technology
Method used
Image
Examples
Embodiment 1
[0041] H in the Claus tail gas of this embodiment 2 The volume concentration of S gas is 2%, SO 2 The gas volume concentration is 1%, the COS gas volume concentration is 1000ppm, and the CS 2 The gas volume concentration is 1000ppm. The volume ratio of oxygen to sulfide in the mixed gas is 2, the volume of water vapor accounts for 10% of the total volume of the mixed gas, and the rest is N 2 .
[0042] Coconut shell activated carbon was immersed in 5% Cu(NO 3 ) 2 In the solution, stand still for 2-24 hours, filter and dry at 150°C for 2-6 hours, and then roast at 200-850°C for 2-5 hours under inert gas to obtain the modified adsorbent. The Claus exhaust gas is mixed with air or oxygen to form a mixture. Put 3.63g of the modified adsorbent into the adsorption bed, pass the mixed gas into the adsorption bed, the operating temperature of the adsorption bed is 60°C, the internal pressure of the adsorption bed is 0.1Mpa, and the space velocity of the mixed gas entering th...
Embodiment 2
[0044] H in the Claus tail gas of this embodiment 2 The volume concentration of S gas is 2%, SO 2 The gas volume concentration is 1%, the COS gas volume concentration is 1000ppm, and the CS 2 The gas volume concentration is 1000ppm. The volume ratio of oxygen to sulfide in the mixed gas is 2, the volume of water vapor accounts for 10% of the total volume of the mixed gas, and the rest is N 2 .
[0045] Immerse the ZSM-5 molecular sieve into Fe(NO 3 ) 3 and a mass concentration of 2.5% Ni (CH 3 COO) 2 In the mixed solution, stand still for 2-24 hours, filter and dry at 150°C for 2-6 hours, and then roast at 200-850°C for 2-5 hours under inert gas to obtain the modified adsorbent. The Claus exhaust gas is mixed with air or oxygen to form a mixture. Put 3.63g of the modified adsorbent into the adsorption bed, pass the mixed gas into the adsorption bed, the operating temperature of the adsorption bed is 60°C, the internal pressure of the adsorption bed is 0.1Mpa, and t...
Embodiment 3
[0047] H in the Claus tail gas of this embodiment 2 The volume concentration of S gas is 2%, SO 2 The gas volume concentration is 1%, the COS gas volume concentration is 1000ppm, and the CS 2 The gas volume concentration is 1000ppm. The volume ratio of oxygen to sulfide in the mixed gas is 6, the volume of water vapor accounts for 50% of the total volume of the mixed gas, and the rest is N 2 .
[0048] The SBA-15 mesoporous molecular sieve was immersed in 5% Cu(NO 3 ) 2 In the solution, stand still for 2-24 hours, filter and dry at 150°C for 2-6 hours, and then roast at 200-850°C for 2-5 hours under inert gas to obtain the modified adsorbent. The Claus exhaust gas is mixed with air or oxygen to form a mixture. Put 3.63g of the modified adsorbent into the adsorption bed, and pass the mixed gas into the adsorption bed. The operating temperature of the adsorption bed is 160°C, the internal pressure of the adsorption bed is 1Mpa, and the space velocity of the mixed gas e...
PUM
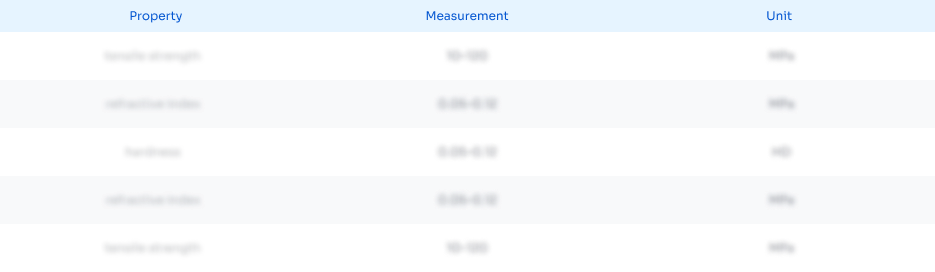
Abstract
Description
Claims
Application Information

- Generate Ideas
- Intellectual Property
- Life Sciences
- Materials
- Tech Scout
- Unparalleled Data Quality
- Higher Quality Content
- 60% Fewer Hallucinations
Browse by: Latest US Patents, China's latest patents, Technical Efficacy Thesaurus, Application Domain, Technology Topic, Popular Technical Reports.
© 2025 PatSnap. All rights reserved.Legal|Privacy policy|Modern Slavery Act Transparency Statement|Sitemap|About US| Contact US: help@patsnap.com