ECF bleaching method for reducing AOX formation amount
A bleaching tower and weight technology, applied in pulp bleaching, textiles and papermaking, papermaking, etc., can solve the problems of unsatisfactory effect, increase of additional investment, consumption of chemicals, etc., to reduce content, reduce pollution, and save usage Effect
- Summary
- Abstract
- Description
- Claims
- Application Information
AI Technical Summary
Problems solved by technology
Method used
Examples
Embodiment 1
[0015] ECF bleaching methods to reduce AOX formation:
[0016] 1. Pretreatment of unbleached pulp with hemicellulase:
[0017] The washed and screened unbleached bagasse pulp is sent to the pretreatment bleaching tower for enzyme pretreatment. The process conditions are: the temperature is 40°C, and the enzyme dosage is 100IU / g 浆 , the reaction pH value is 9, and the reaction time is 90 minutes to obtain bagasse slurry after hemicellulase pretreatment.
[0018] 2. ECF bleaching of bagasse pulp in the presence of chlorine dioxide, sodium hydroxide, hydrogen peroxide and potassium sulfide:
[0019] In the traditional ECF bleaching process D 0 E. p D. 1 Add potassium sulfide in the alkali extraction section of the step 1, and send the bagasse slurry after the hemicellulase pretreatment in step 1 to the chlorine dioxide bleaching tower for delignification after washing. 0 The amount of chlorine dioxide is 1% of the weight of the bagasse slurry after hemicellulase pretreatment...
Embodiment 2
[0021] ECF bleaching methods to reduce AOX formation:
[0022] 1. Pretreatment of unbleached pulp with hemicellulase:
[0023] The washed and screened unbleached bagasse pulp is sent to the pretreatment bleaching tower for enzyme pretreatment. The process conditions are: the temperature is 50°C, and the enzyme dosage is 150IU / g 浆 , the reaction pH value is 10, the reaction time is 100min, and the bagasse slurry after hemicellulase pretreatment is obtained.
[0024] 2. ECF bleaching of bagasse pulp in the presence of chlorine dioxide, sodium hydroxide, hydrogen peroxide and potassium sulfide:
[0025] In the traditional ECF bleaching process D 0 E. p D. 1 Add potassium sulfide in the alkali extraction section of the step 1, and send the bagasse slurry after the hemicellulase pretreatment in step 1 to the chlorine dioxide bleaching tower for delignification after washing. 0 , the amount of chlorine dioxide is 3% of the bagasse slurry weight after hemicellulase pretreatment;...
Embodiment 3
[0027] ECF bleaching methods to reduce AOX formation:
[0028] 1. Pretreatment of unbleached pulp with hemicellulase:
[0029] Send the washed and screened unbleached bagasse pulp to the pretreatment bleaching tower for enzyme pretreatment. The process conditions are: temperature is 60°C, enzyme dosage is 200IU / g 浆 , the reaction pH value is 11, and the reaction time is 120 minutes to obtain bagasse slurry after hemicellulase pretreatment.
[0030] 2. ECF bleaching of bagasse pulp in the presence of chlorine dioxide, sodium hydroxide, hydrogen peroxide and potassium sulfide:
[0031] In the traditional ECF bleaching process D 0 E. p D. 1 Add potassium sulfide in the alkali extraction section of the step 1, and send the bagasse slurry after the hemicellulase pretreatment in step 1 to the chlorine dioxide bleaching tower for delignification after washing. 0 , chlorine dioxide consumption is 5% of the bagasse slurry weight after hemicellulase pretreatment; p , wherein the a...
PUM
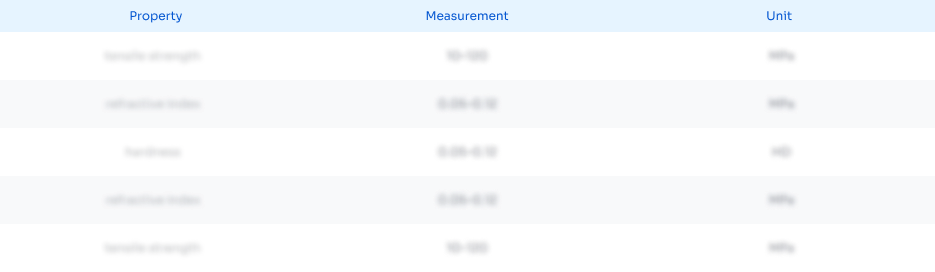
Abstract
Description
Claims
Application Information

- Generate Ideas
- Intellectual Property
- Life Sciences
- Materials
- Tech Scout
- Unparalleled Data Quality
- Higher Quality Content
- 60% Fewer Hallucinations
Browse by: Latest US Patents, China's latest patents, Technical Efficacy Thesaurus, Application Domain, Technology Topic, Popular Technical Reports.
© 2025 PatSnap. All rights reserved.Legal|Privacy policy|Modern Slavery Act Transparency Statement|Sitemap|About US| Contact US: help@patsnap.com