Low-temperature differential thermal control device for infrared horizon sensors of orbit transfer vehicle
An infrared horizon and orbit transfer technology, which is applied in the direction of the device for controlling the living conditions of the spacecraft, can solve the problems of exceeding the target range, potential safety hazards, and approaching working temperature, so as to reduce low-temperature heat leakage, high reliability, and enhanced adaptive effect
- Summary
- Abstract
- Description
- Claims
- Application Information
AI Technical Summary
Problems solved by technology
Method used
Image
Examples
Embodiment Construction
[0026] The present invention will be described in detail below in conjunction with specific embodiments. The following examples will help those skilled in the art to further understand the present invention, but do not limit the present invention in any form. It should be pointed out that for those of ordinary skill in the art, a number of modifications and improvements can be made without departing from the concept of the present invention. These all belong to the protection scope of the present invention.
[0027] The invention provides a low-temperature differential thermal design technology for an infrared horizon meter of an orbit transfer aircraft, which includes heat insulation pad 1, S781 white paint thermal control coating 2, multilayer heat insulation component 3, thermistor 4, and electric heater 5.
[0028] First, paste the thermistor 4 and heater 5 on the heads of the tilting and rolling horizons respectively to ensure that the heater is well attached to the surface ...
PUM
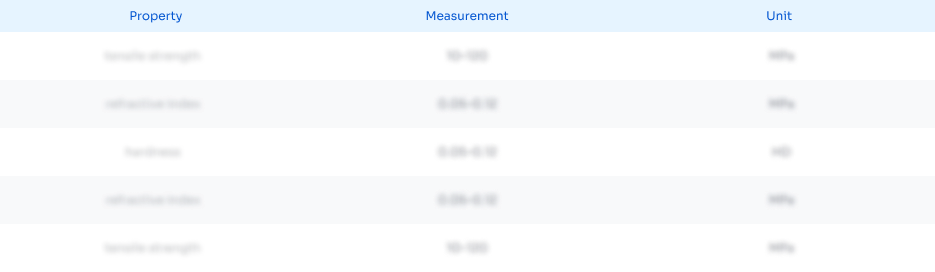
Abstract
Description
Claims
Application Information

- R&D
- Intellectual Property
- Life Sciences
- Materials
- Tech Scout
- Unparalleled Data Quality
- Higher Quality Content
- 60% Fewer Hallucinations
Browse by: Latest US Patents, China's latest patents, Technical Efficacy Thesaurus, Application Domain, Technology Topic, Popular Technical Reports.
© 2025 PatSnap. All rights reserved.Legal|Privacy policy|Modern Slavery Act Transparency Statement|Sitemap|About US| Contact US: help@patsnap.com