Anticorrosive coating
A technology of anti-corrosion coatings and parts by weight, applied in the direction of anti-corrosion coatings, coatings, conjugated diene coatings, etc., can solve the problems of poor anti-corrosion performance, difficulty in guaranteeing the validity period of coatings, and the need to improve the vulcanization resistance of coatings. Impact resistance, strong adhesion at room temperature, and good sulfur resistance
- Summary
- Abstract
- Description
- Claims
- Application Information
AI Technical Summary
Problems solved by technology
Method used
Examples
Embodiment 1
[0015] (1) Weigh 10 parts of film-forming aid, 10 parts of magnesium oxide, 12 parts of silicon oxide, 1 part of iron oxide, 5 parts of toluenesulfonic acid, 5 parts of calcium carbonate, 2 parts of suspending agent, 3 parts of alcohol solvent, 1 1 part of adhesive and 20 parts of deionized water are stirred evenly at a temperature of 60-70 °C at a speed of 400-800 r / min.
[0016] (2) Weigh 50 parts of zinc acrylate resin, 4 parts of phenalkamine, and 1 part of nitrile rubber, add them to step (1), and react in a water bath at 90-110°C for 25-35 minutes while stirring.
[0017] (3) Weigh 0.7 parts of thickener, 0.5 parts of defoamer, and 0.4 parts of leveling agent into step (2), and stir for 10 to 13 minutes at a speed of 200~400r / min; filter to obtain the coating .
Embodiment 2
[0019] (1) Weigh 15 parts of film-forming aid, 20 parts of magnesium oxide, 22 parts of silicon oxide, 2 parts of iron oxide, 8 parts of toluenesulfonic acid, 8 parts of calcium carbonate, 3 parts of suspending agent, 5 parts of alcohol solvent, 2 parts of 1 part of adhesive and 30 parts of deionized water were stirred evenly at a temperature of 60-70 °C at a speed of 400-800 r / min.
[0020] (2) Weigh 60 parts of zinc acrylate resin, 6 parts of phenalkamine, and 2 parts of nitrile rubber, add them to step (1), and react in a water bath at 90-110°C for 25-35 minutes while stirring.
[0021] (3) Weigh 1.2 parts of thickener, 1 part of defoamer, and 0.8 parts of leveling agent into step (2), and stir for 10 to 13 minutes at a speed of 200~400r / min; filter to obtain the coating .
Embodiment 3
[0023] (1) Weigh 12 parts of film-forming aids, 15 parts of magnesium oxide, 17 parts of silicon oxide, 1.5 parts of iron oxide, 6.5 parts of toluenesulfonic acid, 7 parts of calcium carbonate, 2.5 parts of suspending agent, 4 parts of alcohol solvent, 1.5 parts of The adhesive and 25 parts of deionized water are stirred evenly at a temperature of 60-70°C and a speed of 400-800r / min.
[0024] (2) Weigh 55 parts of zinc acrylate resin, 5 parts of phenalkamine, and 1.5 parts of nitrile rubber, add them to step (1), and react in a water bath at 90-110°C for 25-35 minutes while stirring.
[0025] (3) Weigh 0.9 parts of thickener, 0.8 parts of defoamer, and 0.6 parts of leveling agent into step (2), and stir for 10 to 13 minutes at a speed of 200~400r / min; filter to obtain the coating .
[0026] In the present invention, after the paint is sprayed on the substrate, when the sulfur in the air contacts the paint film, under the action of toluenesulfonic acid, the reaction product ge...
PUM
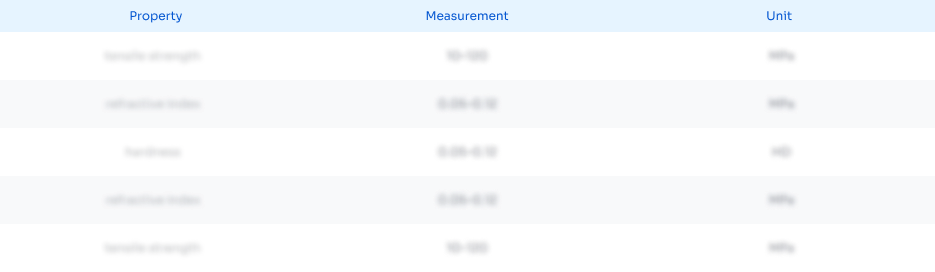
Abstract
Description
Claims
Application Information

- R&D
- Intellectual Property
- Life Sciences
- Materials
- Tech Scout
- Unparalleled Data Quality
- Higher Quality Content
- 60% Fewer Hallucinations
Browse by: Latest US Patents, China's latest patents, Technical Efficacy Thesaurus, Application Domain, Technology Topic, Popular Technical Reports.
© 2025 PatSnap. All rights reserved.Legal|Privacy policy|Modern Slavery Act Transparency Statement|Sitemap|About US| Contact US: help@patsnap.com