Flexible special extinction printing ink containing modified glass powder and preparation method of flexible special extinction printing ink
A glass powder, lead-free glass powder technology, applied in inks, household appliances, applications, etc., can solve the problems of unsatisfactory performance and hidden safety hazards, and achieve accelerated curing, improved environmental protection, and excellent mechanical properties. Effect
- Summary
- Abstract
- Description
- Claims
- Application Information
AI Technical Summary
Problems solved by technology
Method used
Image
Examples
Embodiment
[0011] The ink of the present embodiment is made of the following raw materials by weight: hydroxyacrylic resin 25, lead-free glass powder 3, alkyd resin 35, vinyl n-butyl ether 4, amino silicone oil 3, ethylene glycol diglycidyl ether 6, Cellulose sulfate 4, borax 2, DBE solvent 20, ethyl acetate 14, environmental pigment 22, additive 4.
[0012] The auxiliary agent is made of the following raw materials in parts by weight: polyvinyl butyral 4, silane coupling agent KH560 2, propylenediamine phosphate 0.3, polyamide wax 3, silicone defoamer 2, diethylene glycol ether Acetate 15, nano-starch 6, the preparation method is: first mix the nano-starch and silane coupling agent KH560, grind and disperse for 30 minutes to obtain surface-modified nano-starch for later use, and then mix other remaining materials, stir for 40 minutes, and mix the mixed solution Heat to 60-80°C, add surface-modified nano-starch, stir to disperse evenly, keep warm and ultrasonically disperse for 5 hours t...
PUM
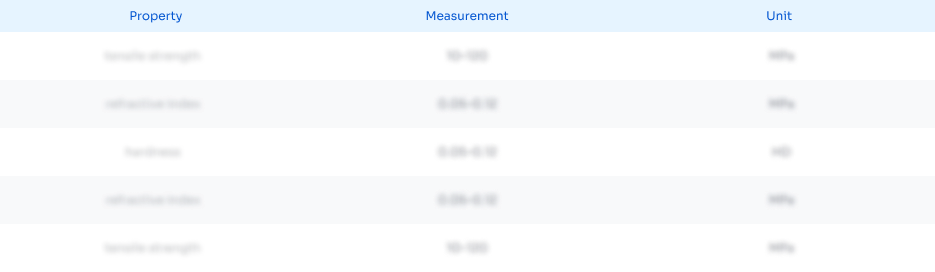
Abstract
Description
Claims
Application Information

- Generate Ideas
- Intellectual Property
- Life Sciences
- Materials
- Tech Scout
- Unparalleled Data Quality
- Higher Quality Content
- 60% Fewer Hallucinations
Browse by: Latest US Patents, China's latest patents, Technical Efficacy Thesaurus, Application Domain, Technology Topic, Popular Technical Reports.
© 2025 PatSnap. All rights reserved.Legal|Privacy policy|Modern Slavery Act Transparency Statement|Sitemap|About US| Contact US: help@patsnap.com