Method for continuously preparing 3,4-dichlorophenyl isocyanate
A technology of dichlorophenylisocyanate and dichloroaniline, which is applied in the field of continuous production and preparation of 3,4-dichlorophenylisocyanate, can solve the problems of waste of phosgene, easy bumping of materials, long cycle, etc., and achieve process performance Less energy consumption and higher production efficiency
- Summary
- Abstract
- Description
- Claims
- Application Information
AI Technical Summary
Problems solved by technology
Method used
Image
Examples
Embodiment 1
[0019] Add 900Kg 3,4-dichloroaniline (content 99%) and 1500Kg dichloroethane into a 3000-liter mixing tank, stir and dissolve evenly, and add 250 liters of them respectively to the 1000-liter reactors A, B and C connected in series Dichloroethane, after stirring and raising the temperature to about 60°C, simultaneously feed phosgene at a rate of 5973 liters (240 moles) / hour, 5475 liters (220 moles) / hour, and 4978 liters (200 moles) / hour (content 90%), dropwise add the mixed 3,4-dichloroaniline dichloroethane solution in reactor A, B, C at the speed of 87.2Kg (200 mol) / hour simultaneously, collect each one continuously after one hour The reaction liquid in the reaction kettle is sent to the exhaust tank, and the nitrogen gas is turned on to drive away the mixed gas containing a small amount of phosgene and a large amount of hydrochloric acid gas in the reaction liquid. The mixed gas enters the low-temperature cooling device and then enters the tail gas absorption system. The pr...
Embodiment 2
[0021] Add 900Kg 3,4-dichloroaniline (content 99%) and 900Kg dichloroethane into a 3000-liter mixing tank, stir and dissolve evenly, and add 250 liters of them respectively in the 1000-liter reactors A, B and C connected in series After dichloroethane is stirred and heated to about 60°C, phosgene is introduced at the speed of 5973 liters / hour (240 moles) / hour, 5475 liters (220 moles) / hour and 4978 liters (200 moles) / hour respectively. (content 90%), at the same time, drop the mixed 3,4-dichloroaniline dichloroethane solution into the reactors A, B, and C at a speed of 65.4Kg (200 mol) / hour. After one hour, continuously collect the reaction liquid from each reactor to the flushing tank, turn on the nitrogen gas, and drive away the mixed gas containing a small amount of phosgene and a large amount of hydrochloric acid gas in the reaction liquid. The mixed gas enters the low-temperature cooling device and then enters the tail gas absorption system. The reaction liquid after being...
Embodiment 3
[0023] Add 900Kg 3,4-dichloroaniline (content 99%), 600Kg dichloroethane in the 3000-liter mixing tank, stir and dissolve evenly, and add 330 kg respectively in the 1000-liter reactors A, B and C connected in series After liters of dichloroethane, stir and heat up to about 60°C, at the same time pass light at the speed of 5973 liters (240 moles) / hour, 5475 liters (220 moles) / hour, 4978 liters (200 moles) / hour gas (content 90%), and at the same time drop the mixed 3,4-dichloroaniline dichloroethane solution into the reactors A, B, and C at a speed of 54.5Kg (200 mol) / hour. After one hour, continuously collect the reaction liquid from each reactor to the flushing tank, turn on the nitrogen gas, and drive away the mixed gas containing a small amount of phosgene and a large amount of hydrochloric acid gas in the reaction liquid. The mixed gas enters the low-temperature cooling device and then enters the tail gas absorption system. The reaction solution after being purged with nitr...
PUM
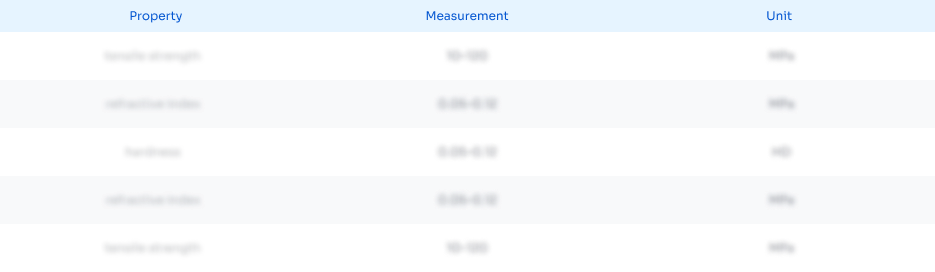
Abstract
Description
Claims
Application Information

- R&D
- Intellectual Property
- Life Sciences
- Materials
- Tech Scout
- Unparalleled Data Quality
- Higher Quality Content
- 60% Fewer Hallucinations
Browse by: Latest US Patents, China's latest patents, Technical Efficacy Thesaurus, Application Domain, Technology Topic, Popular Technical Reports.
© 2025 PatSnap. All rights reserved.Legal|Privacy policy|Modern Slavery Act Transparency Statement|Sitemap|About US| Contact US: help@patsnap.com