All-silicon MEMS device structure and manufacture method thereof
A device and structural layer technology, applied in the field of all-silicon MEMS device structure and its manufacturing, can solve the problems of back-splash damage on the back of the suspended structure, increased processing cost, and affect device performance, etc., and achieves convenient standard process, good air tightness, A simple way to achieve the effect
- Summary
- Abstract
- Description
- Claims
- Application Information
AI Technical Summary
Problems solved by technology
Method used
Image
Examples
Embodiment Construction
[0025] The present invention will be further described below in conjunction with the accompanying drawings.
[0026] 1. MEMS device structure:
[0027] Such as figure 1 , figure 2 As shown, the MEMS device is composed of a substrate SOI silicon wafer 17 , a structural layer 10 formed of silicon on top of the SOI silicon wafer, and a cap layer SOI silicon wafer 16 . The substrate SOI silicon wafer 17 includes a substrate layer 15 , a buried oxide layer 12 and a top silicon layer 11 , and the cap SOI silicon wafer 16 includes a substrate layer 8 , a buried oxide layer 4 and a top silicon layer 6 .
[0028] The substrate SOI silicon wafer 17 includes an anchor point 11, which acts as a movable structure support, and the buried oxide layer 12 at the bottom of the anchor point 11 acts as an electrical isolation.
[0029] The device structure layer 10 is directly bonded to the substrate SOI silicon wafer 17. During the structure etching release process, etching ions in the etche...
PUM
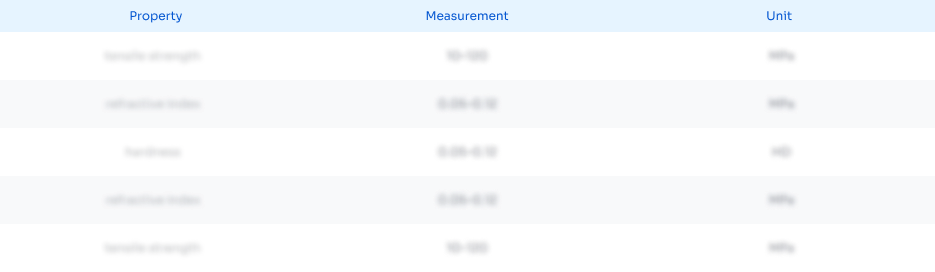
Abstract
Description
Claims
Application Information

- R&D
- Intellectual Property
- Life Sciences
- Materials
- Tech Scout
- Unparalleled Data Quality
- Higher Quality Content
- 60% Fewer Hallucinations
Browse by: Latest US Patents, China's latest patents, Technical Efficacy Thesaurus, Application Domain, Technology Topic, Popular Technical Reports.
© 2025 PatSnap. All rights reserved.Legal|Privacy policy|Modern Slavery Act Transparency Statement|Sitemap|About US| Contact US: help@patsnap.com