High-efficiency coal combustion catalyst
A coal combustion and catalyst technology, applied in the field of high-efficiency coal combustion catalysts, can solve problems such as difficult ignition and heat transfer, reduced thermal efficiency, and large coal heat capacity, so as to ensure combustion conditions and output loads, improve combustion efficiency, and improve combustion efficiency. speed effect
- Summary
- Abstract
- Description
- Claims
- Application Information
AI Technical Summary
Problems solved by technology
Method used
Image
Examples
Embodiment 1
[0025] Take by weight the following raw materials: Triisopropanolamine 5%, Baume degree is 30% of alkali plant waste liquid of 35 ° Bé, tert-butyl alcohol 20%, propylene glycol 15%, lanthanum nitrate 5%, Span-205 %, Tween-205%, isobutanol 6%, NaCl 2%, FeCl 3 7%;
[0026] Add triisopropanolamine, tert-butanol, propylene glycol and isobutanol into the reaction kettle and stir for 50 minutes, then add waste liquid from the alkali plant, stir and mix thoroughly, then add lanthanum nitrate, Span-20, and Tween-20 after filtering , NaCl and FeCl 3 , while continuing to stir, the reactor was heated to 50° C. for 3 hours to obtain the desired coal combustion catalyst.
Embodiment 2
[0028] Take the following raw materials by weight percentage: 7% of triisopropanolamine, 28% of alkali plant waste liquid that Baume degree is 37 ° of Bé, 23% of tert-butyl alcohol, 13% of propylene glycol, lanthanum sulfate 4%, fatty acid glyceride 6 %, Tween-405%, isobutanol 5%, NaCl 3%, FeCl 3 6%;
[0029] Add triisopropanolamine, tert-butanol, propylene glycol and isobutanol into the reaction kettle and stir for 50 minutes, then add waste liquid from the alkali plant, stir and mix thoroughly, and then add lanthanum sulfate, fatty acid glyceride, Tween-40, NaCl and FeCl 3 , while continuing to stir, the reactor was heated to 50° C. for 3 hours to obtain the desired coal combustion catalyst.
Embodiment 3
[0031] Take by weight the following raw materials: Triisopropanolamine 10%, Baume degree is 25% of alkali plant waste liquid of 38 ° B é, tert-butyl alcohol 25%, propylene glycol 12, lanthanum nitrate 3%, Tween-80 12% , Isobutanol 4%, NaCl 4%, FeCl 3 5%;
[0032] Add triisopropanolamine, tert-butanol, propylene glycol and isobutanol into the reaction kettle and stir for 50 minutes, then add waste liquid from the alkali plant, stir and mix thoroughly, and then add lanthanum nitrate, Tween-80, NaCl and FeCl after filtering 3 , while continuing to stir, the reactor was heated to 50° C. for 3 hours to obtain the desired coal combustion catalyst.
PUM
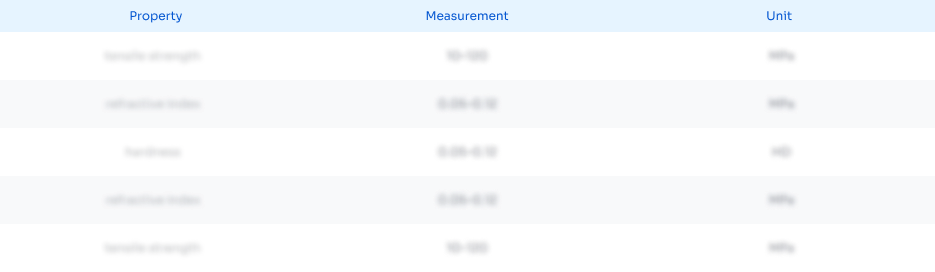
Abstract
Description
Claims
Application Information

- R&D Engineer
- R&D Manager
- IP Professional
- Industry Leading Data Capabilities
- Powerful AI technology
- Patent DNA Extraction
Browse by: Latest US Patents, China's latest patents, Technical Efficacy Thesaurus, Application Domain, Technology Topic, Popular Technical Reports.
© 2024 PatSnap. All rights reserved.Legal|Privacy policy|Modern Slavery Act Transparency Statement|Sitemap|About US| Contact US: help@patsnap.com